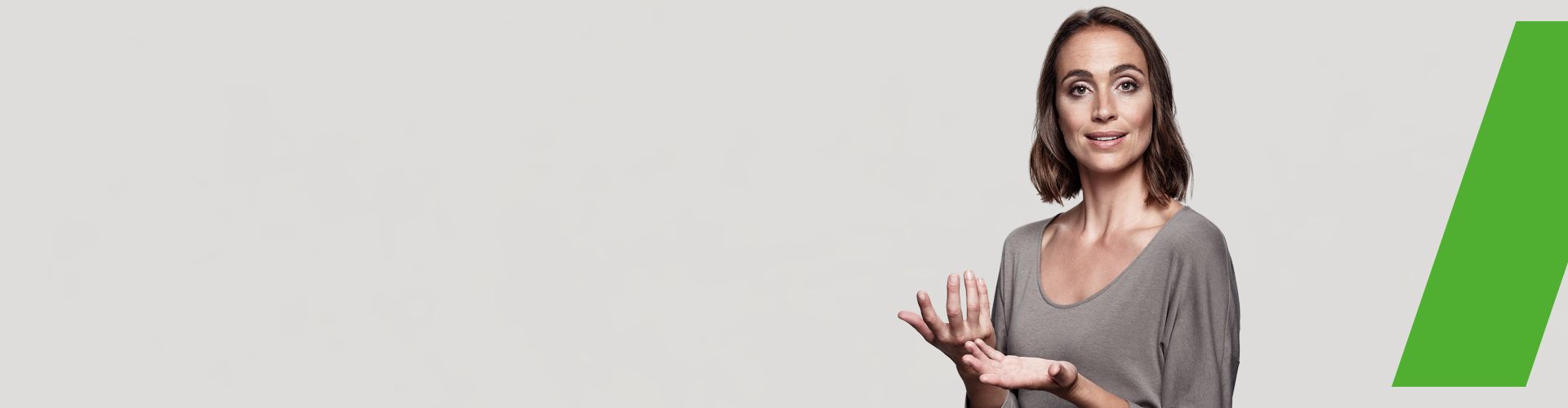
FAQs
Do you have questions on the topic of digitalization, Industry 4.0, and the solutions provided by KEBA? Here, we have collected answers to the most frequently asked questions for you.
Industry 4.0 means the intelligent networking and autonomous control of the production resources and the planning and control systems in the goods-producing sector.
RWTH Aachen University in Germany has developed an Industry 4.0 Maturity Index in cooperation with prominent partners. Its purpose is to help organizations identify their current status and use it as a basis to derive targets for their own development path towards Industry 4.0. The Maturity Index includes four levels and takes a holistic view of an organization's entire value creation process from development, logistics and production to service and sales.
The cloud is a network of computer systems that are connected through the internet and that together provide resources and services. Users can use these resources and services by requesting them through the internet; these resources and services do not need to be available on the users’ own computers or on local networks. Cloud services can encompass data storage, databases, applications and computing power. There are many providers of cloud services, including some of the biggest and well-known companies in the IT industry. These providers offer a multitude of services, such as virtual machines, data storage, databases, networking and security features, development and analysis tools, and many more. There are also many smaller providers offering specialized services, such as solutions for the industrial sector.
It is unlikely that OPC UA will completely supplant EtherCAT. Both technologies have their individual strengths and areas of application. EtherCAT is an Ethernet-based field bus system specializing in the fast, reliable transmission of data in automation engineering. It is particularly well suited to applications that place high demands on real-time abilities and is widely used in industrial automation. OPC UA (Unified Architecture) is an open standard for the communication between devices and systems in automation engineering. It can work via Ethernet as well as other network types such as Wi-Fi, Zigbee or Bluetooth and offers enhanced security and data modeling abilities. OPC UA is more versatile and can be used for a broad range of applications including cloud integration and the connection of IT and OT systems. For this reason, it is likely that OPC UA and EtherCAT will continue to be used side by side, depending on the requirements of the specific situation.
Condition monitoring (CM) refers to the monitoring of the condition of machines and systems. Such solutions are able to detect critical events and indicate them in a suitable manner.
Predictive Maintenance (PdM) is, in a sense, based on condition monitoring. It predicts risks based on the collected experience values and thus allows for the optimal planning of maintenance operations. The difference, then, is in the interpretation. The data basis (CM) is used to make a prediction (PdM).
In short, digitalization brings new market opportunities and can help to differentiate products. But at the same time it necessitates far-reaching further development of the company’s organization in many aspects.
It’s becoming increasingly challenging for the mechanical and plant engineering industry in Europe: price pressure from Asian competitors, the growing shortage of skilled workers, new industry and security norms that have to be met.
Especially small and medium-sized enterprises face problems to handle all these topics.
Digital technologies can theoretically alleviate many of these challenges. With regard to the market, price disadvantages can be compensated by outstanding service and customer benefits, which are based on digital business models, among other things. However, the acceleration of entrepreneurial decision-making and adaptation processes are also a prerequisite for being able to adapt quickly enough to the changing market. The necessary transformation from hardware manufacturer to service-oriented service provider does not stop at product development. The necessary combination of product, service and customer-oriented value proposition requires further development not only in the market-oriented design fields, but also in the value creation processes, the organization, the people, the data consolidation and the corporate culture.
What advantages does digitalization bring to industrial production?
Digitalization offers numerous advantages for industrial production. Some of these are higher efficiency, quality enhancement, more flexibility, safety and cost savings.
Increased efficiency: Through digitalization, production processes can be automated and optimized, leading to higher efficiency. As a result, production time can be reduced, which can lead to faster time-to-market for products.
Enhanced quality: Digitization makes it possible to improve the quality of products through the use of sensors, automated testing processes and real-time data monitoring. As a result, errors and defects during production process can be quickly detected and corrected.
Cost savings: Digitalization enables better monitoring of resources and energy consumption, which can lead to cost savings. The automation of processes can also reduce personnel costs. Hardware elements can be replaced by digital ones, thus reducing acquisition and maintenance costs. Costs in the development phase and commissioning can also be reduced through simulation, for example.
Flexibility: Digitization enables greater flexibility in production, as it makes it possible to quickly adapt production processes and respond to changing requirements.
Increased safety: Digitization makes it possible to perform dangerous or inaccessible tasks through robots or automation. This reduces the risk for employees and increases occupational safety
Better planning: Thanks to digitalization, production processes can be better planned, leading to greater predictability of bottlenecks and delays. Through measures such as condition monitoring and predictive maintenance, anomalies in production plants can be detected in time and maintenance measures can be optimally planned.
In today's manufacturing processes, controllers (PLCs) enable the automation of processes. Repetitive work steps can thus be carried out independently by machines. Automated systems implement predefined sequences of actions, but neither "understand" their consequences nor can they change them. The Industry 4.0 vision envisages fully automated and digitally networked production (smart industry) in which decisions are made and implemented without human intervention. Action sequences are thus not only implemented automatically, but also controlled autonomously. Without human intervention and without resorting to detailed programming, the system reacts to changing conditions and adapts autonomously. This also includes the ability to adapt to human behaviour in human-machine interaction.
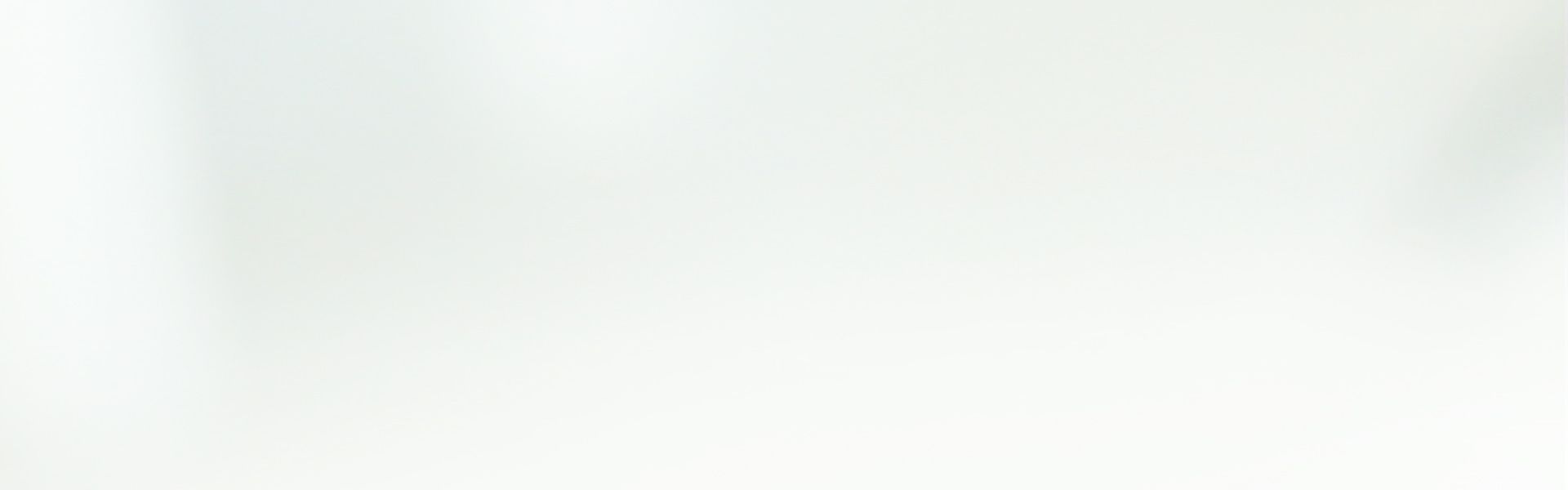
Thank you for your request. Our KEBA Customer Support will get in touch with you soon.
Locations
Business Areas
Newsroom

Edge

Chrome

Safari

Firefox