„Closing the loop“ with innovative hardware and software concepts
- News
- References / Success Stories
- Plastics
- 12.1.2024
- Reading Time: 9 min
- Share Article
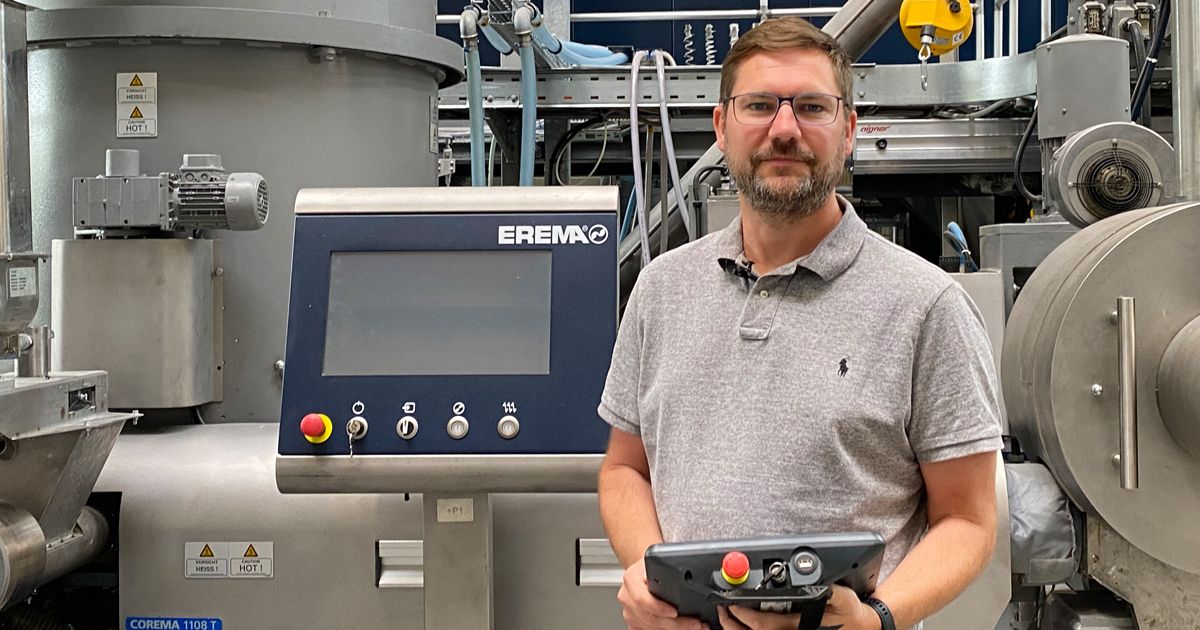
Contents
Successful development project despite world crises
The visionary concept for those who think big
The human factor as a differentiator
Recipe for success for the circular economy: everyone should start with themselves
Current trends in the recycling market
EREMA is the world market leader in manufacturing plastics recycling plants with headquarters in Ansfelden, Upper Austria. Worldwide, the approximately 7,500 plants in operation process more than 20 million tonnes of high-quality granulate annually.
Successful development project despite world crises
There is an old saying that the road to success is paved with challenges, and the cooperation between EREMA & KEBA was no different. The first talks between the two project teams took place back in 2017, the project start was planned for 2019, when the global market situation, the mood, and the requirements were still very different from today. A proven way to get through difficult times is motivation and commitment, which were present on both sides and led to the introduction of KEBA solutions for the Intarema machine series at the K-Show fair in 2022.
"Initially, we were looking for a control technology manufacturer with whom we could flexibly shape our future and who offered total solutions. KEBA was not on the radar at first, but after some research, including discussions with business partners, the perfect win-win situation crystallized due to the good references, the similar size, and the possibility to access development on a partnership level," Martin Kienbauer, Head of Automation at EREMA, explains the beginning of the cooperation. "It was quite a good fit, and so we started the discussion and saw the first results relatively quickly." EREMA wanted to build completely new hardware and no longer just "parameterize" the software but really program it, develop its own architecture, have more freedom and bring its own creativity into the development of the software concepts.
"A big plus for KEBA during these years was that we not only got along well on a technological level but also a human level. The physical proximity, the openness, and the similar mentality were another decisive plus for the successful cooperation," says Kienbauer. The mentality of the KEBAns perfectly explains the "KEBA DNA formula" and defines it as a unique mixture of creativity, enthusiasm, determination and enjoyment of working together. Finding these qualities on both sides is undoubtedly a prerequisite for a lasting partnership.
With the global supply chain crisis starting in 2021, these characteristics suddenly played an essential role - together with KEBA's ability to deliver products on time thanks to agile supply chain management, including the Austrian production facilities.
One of the lessons learned from the crisis, not only for EREMA but for the entire industry, is to consider a two-supplier strategy in order to achieve smooth, continuous operation. Developments in recent years, especially in the field of automation, have shown that procurement has become more risky. It is definitely a new reality for some companies - both on the customer and supplier side.
The visionary concept for those who think big
"Companies are often trimmed for years to think the way the main supplier thinks, and this brings a certain inflexibility or leads to blind spots," says Kienbauer. "KEBA brought in new perspectives and helped to launch a visionary, ground-breaking project to develop a completely new automation concept for EREMA," Kienbauer continues.
Untypically, the main driver for developing this new concept was not saving costs. "Of course, costs are always an issue, but we, as technological pioneers, are driven by other things. The first driver and the absolute main reason was the move away from parameterization and into real programming to take things into our own hands, i.e., to program, to visualize, to design something completely new in-depth ourselves," Kienbauer explains.
The implemented concepts are based on the KEBA Kemro X automation platform, in a decentralized hardware concept, their focus is on the systematic construction of a modular machine architecture. The idea is to replace a central control with several compact controls from the scalable KeControl C5 control family in order to establish more flexibility for customer requirements. Optional peripheral units can either operate independently or be seamlessly integrated into an overall EREMA system. Modern software structures of the Kemro X platform and state-of-the-art technologies such as OPC UA Pub/Sub support this solution approach. Future-proof technology and programming, openness to developing own services at the control level, and integration into the EREMA Bluport portal - the EdgeDevice solution - are also essential components of the architecture.
A modern multi-touch HMI panel from the KeTop AP500 series is used as the visualization device. The large 21.5" multitouch screen with a powerful Windows 10 IOT operating system offers enough space for efficient and modern operation. For larger recycling sites, there will be several such panels in use.
An additional benefit of this HMI approach is that it will also be possible to access mobile devices of the KeTop family in the future - a circumstance that appears to be very interesting, especially with the ever-larger EREMA machine systems.
"It wasn't clear whether the project would turn out 100% the way I imagined, but it was important to me that you can look a bit beyond the horizon and think big," says Kienbauer. Another factor in the success of the development process was the excellent communication and openness on both sides - the teams went "all-in" and did not shy away from addressing conflicts or unpleasant topics.
The human factor as a differentiator
One thing that none of the automation solution providers can ever automate is the chemistry between people. Even in this day and age when many people find themselves talking to AI assistants more than family members on some days, nurturing a company's culture, its “DNA”, and building personal relationships within an organization as well as with customers is just as important as developing the latest cutting-edge technologies.
Kienbauer says: "Technical things are all important, but you can catch up on them somehow. What I find at least as important is that you can always get in touch if you need something, that you can call, that you can rely on partners, that you treat each other with respect, and that you value each other. That shows a certain quality for me." EREMA and KEBA hit it off - not just the business and technological goals but also the values, personal motivation, and desire to create incredible innovations - across the entire cross-functional project team, from top management to sales and product management to engineers and software developers. "It's more than a customer-supplier relationship. I see it as a partnership that benefits both sides because we can learn from each other technologically. In the HMI area, for example, we have understood that we need to build our software architecture differently and can benefit from this," adds Kienbauer.

© KEBA
Recipe for success for the circular economy: everyone should start with themselves
When addressing the topic of recycling and the circular economy, the discussion should go beyond the capabilities of machines and technology. According to Kienbauer, there is no universal recipe for how to solve the current problems and be globally successful, but one thing is clear: everyone should start with themselves. For EREMA, it is not just about the number of machines produced and sold but about what happens to them and what contribution they can make. Even though the company has become known for its plastic recycling plants and machines, other companies in the EREMA Group play their own role in EREMA's journey to close the loop of the economy. For example, the company Plasticpreneur's mission is to create affordable access to small-scale plastics recycling worldwide that can benefit local communities environmentally, socially, and economically.
According to Kienbauer, there are still common misconceptions about the perception of plastics as a material. Kienbauer: "Many people think that plastics are only bad in every way and that life would be better without plastics." He acknowledges that waste pollution is a global problem with much room for improvement. "For us, two things are essential. Firstly, that we stay hungry for new innovations, and secondly, that the end customer knows what can be done with the product they buy in terms of recycling so that things are not just thrown away," says Kienbauer.
Current trends in the recycling market
Despite the difficult global market situation, investments in recycling plants seem to be "in", as EREMA's turnover has increased in recent years, partly due to new favorable EU regulations and EU policies as a whole but also due to new customer structures in the market. In the past, there were many small recycling companies that did everything on their own, locally, and on a small to medium scale. Recently, however, more well-known and globally active companies have become interested in EREMA's products, and other solutions for recycling film production waste or chemicals are also on the rise. Global brands such as Coca-Cola have set a target of 50% recycled content in plastic bottles by 2025 (source: Packaging Gateway, 2023) - and other well-known brands are following the trend of including recycled plastics in product/packaging recipes. These trends, driven by the consumer market, are having an impact on global recycling machine sales. With the vast majority of plastic products, including packaging, being manufactured locally on all continents, demand for recycled plastic granules and machinery to produce them is increasing, especially in Europe, South and North America, Africa, and Asia.
When increasing quality requirements motivate
Increasing quality requirements are another challenge, but Kienbauer also sees this as an opportunity: "Every quality improvement we achieve means that the granulate can most likely be used in new products, and it provides a broader base for new applications." Each manufacturer's product group has its own ideas of quality, needs, and priorities. Water bottles have different quality requirements than shampoo bottles or packaging for cheese or ham. With the constant increase in quality requirements, the effort to rethink and redesign internal processes as well as to work with more flexible suppliers also increases, but this does not deter Kienbauer and his team. "Therefore, it is a great challenge that motivates me to do more, and I am glad that there are business partners like KEBA who enable progress and understand needs in our industry."
The future of EREMA & KEBA
Even though the events of the last few years have taught us that planning far into the future is becoming increasingly difficult, KEBA and EREMA can nevertheless draw up some plans. The next concrete steps are, in addition to the introduction of the existing solutions for the Intarema machine series and peripherals (e.g., the filtration device), continuous cooperation on technology topics and further developments, as well as an analysis of the possible applications of KeTop Wireless HMIs. In addition, further consideration is being given to how Kemro X, KEBA's open control platform, can be used to incorporate all technologies and benefits directly into the control system itself.
"I am glad that there are business partners like KEBA who enable progress and understand needs in our industry."