Rotary indexing machines: the next level in machine operation
- News
- References / Success Stories
- HMI
- 16.5.2023
- Reading Time: {{readingTime}} min
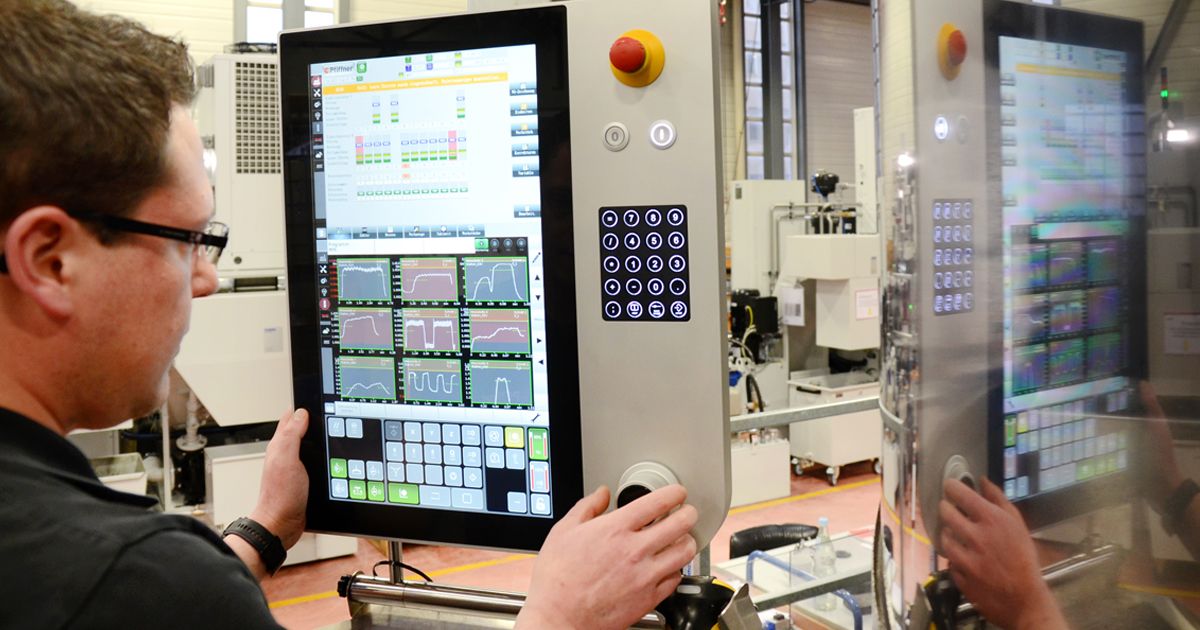
Contents
Pfiffner and Witzig & Frank (the Pfiffner Group) with headquarters in Utzenstorf, Switzerland, are part of FFG E&A, which is part of the globally active Fair Friend Group. It combines 15 established German, Italian, Swiss and American manufacturers of metalworking lathes, milling machines, rotary indexing machines, etc. FFG products are used by companies in the automotive sector, aviation and aerospace engineering, machine manufacturing, metalworking, the energy sector and many other industries. With a workforce of 250 employees, the Pfiffner Group makes about 70 million Swiss Francs of revenue annually.
The next level in machine operation
The two companies, Pfiffner and KEBA, first got to know each other at a trade fair, which is not uncommon in this industry. The location was the EMO trade fair, the year was 2017. Tobias Flaig, electrical engineer at Pfiffner: “At the time, we were looking for ideas and concepts for full-touch operating displays, because the industry trend was clearly heading that way. At the EMO, we came to know KEBA and found out that the Austrian automation specialist had already developed some concrete approaches.” KEBA engineers demonstrated the KEBA panel and the engineering details underlying the concept. “Our Director of Development was quite impressed, both with the conversation and with KEBA’s approach,” says Mr. Flaig. “When our supplier at the time discontinued the existing panel product, things happened very quickly at our end.”
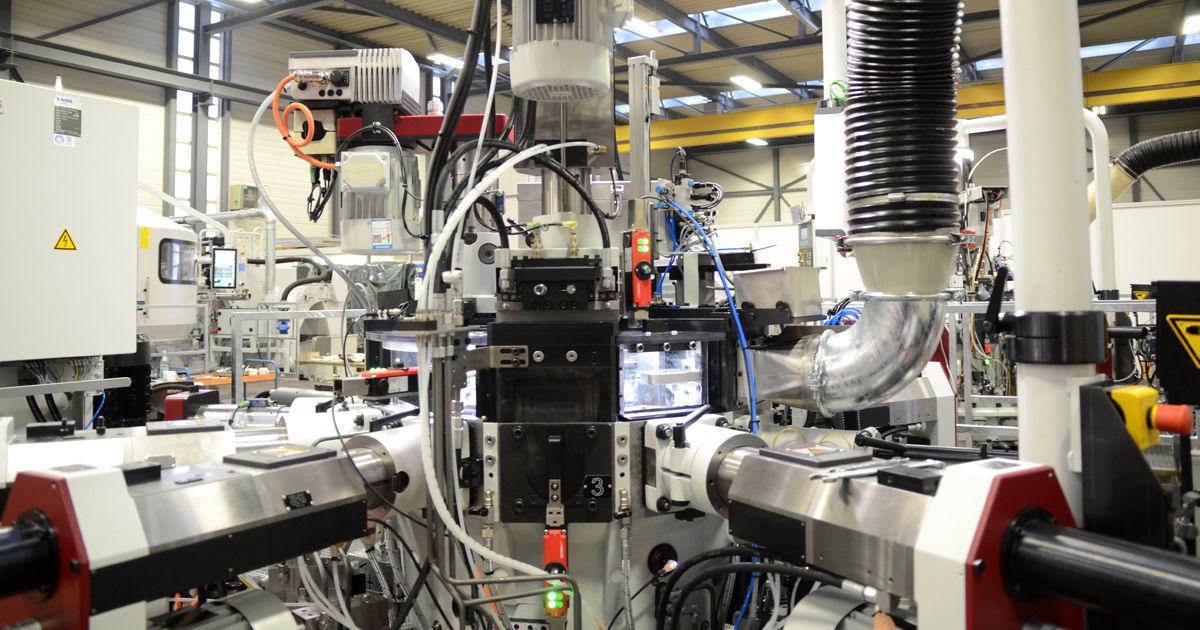
Recipe for success:
Real time widgets and secure communication via PROFINET.
A development project together with the previous supplier would not have been worthwhile, according to Pfiffner. With regard to the state of the art, KEBA was already much more advanced.
Pfiffner embarked on a development project “from scratch” with the UX design as the starting point. An external UX design firm was contracted to develop a completely new user interface in cooperation with KEBA. The project included a close examination of the processes and incorporated feedback provided by Pfiffner employees. The team then used KEBA’s KeView Style visualization software to create a framework application that also takes care of window management and machine operation.
Says Mr. Flaig: “A common problem with full-touch screen displays is that the touch buttons are passed to the controller via OPC UA, which is not secure. The strength of KEBA’s solution were the so-called real time widgets, which make sure that all buttons of the machine operation device are passed to the PLC controller via PROFINET.” The hardware buttons of old were implemented as identical soft keys. Says Mr. Flaig: “What was special about this solution was the fact that these soft keys are real-time enabled and can be transmitted to the controller in real time: they are written to the PLC via the PROFINET controller. Simultaneously, OPC UA exists as a second channel. This provides for secure communication with the PLC using soft keys.”
Adding yet another twist: KeWheel
Another crucial factor for the decision to partner with KEBA for the development of the next-generation HMI was the KeWheel. The KeWheel is a fully adaptive rotary push button. Using the KeWheel as the main operating element, items such as overrides, hand wheels, mode-selection switches, axis travel buttons, and user interface inputs can be combined in a single device. The KeWheel provides the operator with additional information about the condition of the machine through a broad range of haptic feedback. Says Mr. Flaig: “We were seriously intrigued by the KeWheel and its options right from the start. Until then, we had two overrides, one for feed and one for spindle, and we combined these two in the KeWheel. We plan to add more operator functions to the KeWheel, for example using it as a handwheel—there is still more potential we can utilize.”
Communication as equal partners
In order for such a comprehensive project to succeed, the relationship must be solid. “We noticed relatively quickly that everybody at KEBA is extremely competent and knowledgeable. We received answers to every question we asked, no matter how detailed. We started having this feeling right at the first conversation, and after that it only grew stronger. When we visited KEBA, we were able to see and feel KEBA’s mentality and work ethic, and afterwards, everybody was even more motivated!”, says Mr. Flaig.
Of course, there were also some obstacles in the project. The biggest issue was the fact that Bosch Rexroth Operations had to be integrated—previously, Bosch Rexroth was the software master, but this time it was the other way round: the KEBA framework integrated the Bosch Rexroth system. “A project of this scope does have its quirks, of course, but we handled them or will handle them precisely because the communication is so excellent,” says Mr. Flaig.
We were able to see and feel KEBA’s mentality and work ethic, and afterwards, everybody was even more motivated!
Rotary indexing machines in the manufacturing sector
Rotary indexing machines are machine tools in which the workpiece is clamped into a horizontal or vertical rotary indexing table. They are particularly suited to the mass production of quantities of 250,000 or more. Michael Ensel, Technology Sales Manager at Pfiffner: “Our rule of thumb is: With a processing time of 15 seconds, one machine can produce approximately 1.2 million parts per year.”
Pfiffner customers manufacture a variety of components ranging from electronics to housings for drive components, and they supply their goods to different industries: lock & key engineering, e-mobility, gas & welding engineering, electronics and communication etc. Machines made by Pfiffner can be used to produce components about the size of a fist (cube with an edge length of 100 mm). For larger components, machines made by Witzig & Frank—another company in the group— can be used. Says Mr. Flaig: “We are receiving more and more requests for electronic components that are generally becoming ever more complex; it is no longer possible to just punch them. Our largest customer at the moment is a manufacturer of plugs for the high-frequency range.
The benefits of rotary indexing machines are firstly that less space is needed, because one system can replace multiple conventional systems; and secondly significant cost savings, because one system also means that energy (only one cooling system), consumables, spare parts and service are only needed for one system. In addition, there is only one point of contact on the supplier side and only one process to be monitored and approved by the end customer, which is especially important in the automotive industry where every production system must be approved by the end customer. Typically, one machine operator can operate two, three, up to five rotary indexing machines. Says Mr. Ensel: “There is no specific number of conventional machines that can be replaced by a rotary indexing machine. For a customer in Kazakhstan, for example, we set up two machines that allowed them to retire 38 individual conventional machines.”
The most important pain points for Pfiffner’s end customers are unit costs and precision. Says Mr. Ensel: “The workpiece tolerances are typically in the micrometer range. Our machines have 12 or 16 clamping stations and up to 24 processing units. This makes it extremely important that each station is aligned as precisely as possible.”
The materials to be processed are not an obstacle for rotary indexing machines—they can handle even difficult-to-machine materials. “I have been with Pfiffner since 2014, and during this time we have never had to refuse a request because we considered the material impossible to machine,” says Mr. Ensel.
The Pfiffner engineers, too, must listen closely to their customers needs and develop solutions that address those. Right now, Pfiffner is putting the finishing touches on a software that allows customers to reconfigure their own machines. Previously, Pfiffner took care of reconfiguring NC control systems, drives, etc. via teleservice. Now, operators can do it themselves as part of the retooling process—and frequently used programs and settings can be saved as favorites.