How a logistics solution provider ensures speed and flexibility.
- News
- Robotics
- References / Success Stories
- Intralogistics
- Drive Technology
- 14.10.2022
- Reading Time: {{readingTime}} min
- Share Article
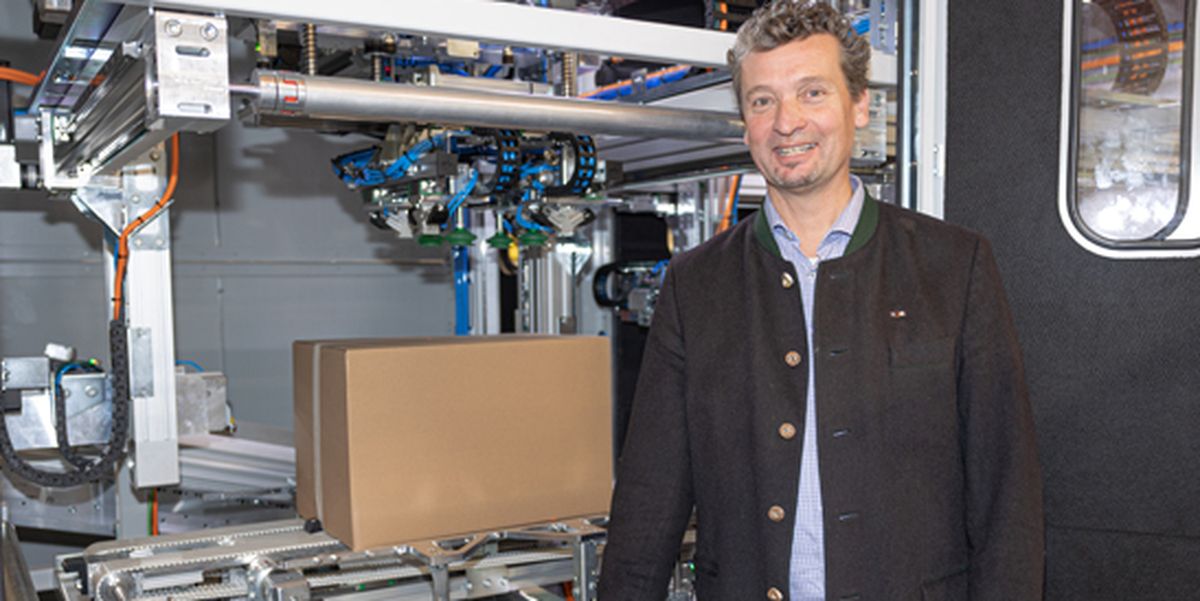
Contents
The logistics industry is facing a lot of challenges right now because it is booming—booming like crazy. E-commerce is thriving, not least driven by the COVID pandemic, but at the same time it needs to be able to react quickly and adapt to new requirements. TGW Robotics GmbH specializes in the development and realization of highly complex custom solutions for intralogistics, robotics, and special conveyor systems. Their product portfolio includes gripping, palletizing and depalletizing solutions as well as carton handling. And they need to be able to respond with the same speed and flexibility as their partners whom they provide with solutions.
Challenges in the logistics industry
The astounding e-commerce boom is changing things. The number of purchase orders for individual items is seeing a heavy increase. Even before the pandemic, some parts of the industry experienced growth rates around 30%, and today, even more business is being triggered by pandemic-related consumer behavior: customers order more items, more regularly and more quickly—in other words they want to receive more items to choose from because trying out items at the store is not always possible or is viewed as inconvenient. In addition, even people who used to shop exclusively at brick-and-mortar stores now order online, perhaps out of necessity. Stefan Holzner, Senior Technical Consultant & Patents at TGW Robotics in Germany, is observing these changes from a front-row seat. “There are many changes, and they have a great impact. Many carrier companies have moved beyond just carrying goods and have branched out more and more into operating distribution and logistics centers.” In such cases, TGW provides on-site teams that help operate the plant because initially, many carrier companies lack the required know-how.
Adds Holzner: “New business models are emerging that use very different processes from the ones we’ve known so far—just think of grocery orders delivered right to people’s front doors. This is different from before: the delivery chain reaches from the manufacturer all the way to the customer. Flexibility on the last mile is crucial, and many manufacturers want to control this part. As a result, many brands now do their own deliveries, sometimes even with their own fleet. They are adding this last mile to their service offering in order to be able to deliver as quickly as possible.” Because customers’ expectations have also changed. More and more, they are looking for “ordered today, delivered yesterday”. One effect is that multiple vehicles drive to the same address on the same day—in the past, all of this was taken care of by the postal service. Another trend is the growing frequency of sales peaks in e-commerce, emphasizes Holzner. “Easter and Christmas you can largely plan for, but ‘Black Fridays’ and ‘super sales’ are happening more and more frequently—the logistics industry needs to be incredibly flexible.”
Intralogistics pain points and TGW Robotics solutions
The mantra of the logistics industry is: more speed, precision, compactness and flexibility. This also applies to TGW Robotics and their business partners. TGW Robotics and KEBA have been collaborating since 2017. The first project that the companies worked on together was the optimization of a single-pick method for automated picking. The goal was to enable two simultaneous picking processes by recognizing two source and target boxes at the same time—the robot moves without interruption, the box recognition alternates.
Martin Drexler, KEBA’s sales representative for TGW Robotics: “This required a custom-designed axis solution that coordinates and moves the six axes in space without wobbling despite the high speed. The challenge was the particular arrangement of the mechanical axes for optimal coverage of the rectangular movement space including the edges.” A solution involving a larger standard robot was out of the question. While such a robot would have been able to move along the entire distance, the size of the movements would have made it undynamic so that the required precision and control would no longer be achieved.
KEBA was able to build an extremely compact solution - dubbed “Rovolution” - which allowed for very short distances from the safety fence. Says Holzner: “KEBA’s approach enabled us to complete one entire pick in under four seconds - an outstanding value.” The requirements also included an easy-to-program system using a standard programming language (IEC) and with great flexibility for extensions and add-ons to support the integration of customized software. Says Drexler: “In addition, a fundamental prerequisite was the use of a Siemens controller, which we solved through the Profinet slave option in our motion controller.”
Cartons: sustainable reduction
When it comes to cartons for packaging, trucking companies typically have a number of basic sizes available—the standard sizes are rarely the best fit, so the cartons are cut to size or reduced in height after they have been filled. Says Georg Trenker, product manager for PackChain cartoning machines at TGW Robotics in Germany: “Cartons are a pain point for every single carrier company. The better they can adjust the size of the packaging to the content, the less space is needed on the truck - the effect is immediate. In addition, every trucking operator is looking to reduce the number of basic sizes.” The goal of the project was to create 20 percent less volume, which would effectively mean 20 percent less space needed on the truck. Says Trenker: “There is enormous potential here with an extreme effect on cost - and it is not just about reducing the volume. We also set ourselves the goal of completely eliminating the filler material.” The issue with the filler material is not just one of sustainability, it is also about the experience when the customer opens the box: what will I find and how long will it take me to spot the items I actually ordered? The aesthetics play a big role here. Says Trenker: “Our carton height reducer is now able to cut the size down to as little as 50 mm. This also reduces the shipping cost because in some countries, such as Switzerland, there is a large price increase as soon as the height of a package exceeds 50 mm.
Opening cartons: manual effort and safety hazard
Another work step for which TGW Robotics needed a custom solution is the cutting open of cartons after they have been received. Says Holzner: “The particular challenge was the large number of manual work steps which, in spite of protective measures, still entail a great risk of injury.” The developers at TGW Robotics in Stephanskirchen in Bavaria came up with a concept for the fully automated cutting open of cartons. Their goal: firstly zero injuries, and secondly more speed by completely eliminating manual work steps - at a rate of 900 cartons per hour. Says Holzner: “This task was really tricky because of the fact that the cartons that arrive don't follow any standards for sizing and in addition, the cartons may have been damaged or deformed in transit.” In other words, when it comes to goods receipt, each carton is unique. The solution offered by TGW Robotics ensures that each carton is measured before it is opened. The axes are adapted to the dimensions of the respective carton. A sizing unit uses a camera system to measure any deviations or irregularities with respect to length, width and height. This allows the blades to cut open the carton lid with high precision and without damaging any of the contents.
Technology: what it’s all about
For the carton height reducer and the carton opener, it was again about the simultaneous movement of many axes. Says Holzner: “Standard industrial robots were not suitable and we needed a custom gantry solution that would be simultaneously flexible and compact enough to achieve our goals.” Not a trivial task for a cycle rate of 900.
Says Holzner: “KEBA drives are much smaller in size than competitors’ products. This compact design is unique—without it, we would have had to redesign everything.” And such a redesign would have meant building a bigger and more robust system, requiring compromises with regard to dynamics, precision and speed and taking up more space. Adds Drexler: “For the carton height reducer and the carton opener, we are talking about 19 axes in total. The multi-axis system made it possible to implement this application in a very compact format. The system controller, a 10-kW power supply unit and seven axis controllers with three axes each fit into a cabinet that is not even 50 cm wide!” This has raised the bar really high.
TGW Robotics decided to equip all machines in carton packaging with KEBA technology. Aside from the carton height reducer and the carton opener which have already been modified, this also includes the carton erector and the carton lidding machine. Holzner is looking to the future: “We might also use it for gantry systems. They involve complex movements in space where time and again, we are confronted with performance limitations due to the motion.”
Cherry on top: smart simulation model as bonus
Another important aspect for TGW Robotics is knowledge transfer, both within the TGW group and also with customers. Says Holzner: “In-house, we were thinking about how best to teach the new philosophy, which robot would be best suited to that purpose, etc. and based on that, KEBA came up with the idea of building a simulator.” It provides the flexibility to offer training internationally without any major investment in a specific type of robot. KEBA was provided with the 3D data for a visual representation. The simulation model makes it possible to program movement models, to simulate and to optimize them. Life-time services, maintenance, the replacement of axes etc. can also be simulated. Says Holzner: “A physical system would have been very expensive. Also, we would have had to pick just one model, which would have included a high risk potential. The simulation model developed by KEBA is extremely simple and very inexpensive.” During the first stage, TGW Robotics uses the simulation for in-house training teaching KEBA technology. Says Holzner: “The simulation tool allows our workers to become familiar with KEBA technology. This gives them the confidence to start working on the actual machine and assist with the monitoring and start-up of the system. The next stage is to use the simulation tool for customer training.”
The result of the cooperation with KEBA: tailor-made logistics solutions and a partnership on eye-level.
Out-of-the-box solutions available on the market were not an option for TGW Robotics. They needed a partner who develops tailor-made solutions and fulfills certain requirements. Says Holzner about the cooperation with KEBA: “Something that’s great about KEBA is that they have points of contact with solid engineering competence and who don't change all the time. When you call them on the phone, you get to talk to the right point of contact who can suggest a solution for your issue. At other companies, they assign you a support ticket...” Another thing that TGW appreciates about KEBA - aside from the fact that KEBA was able to provide a complete solution for the task at hand - is their great flexibility and excellent support during the project and start-up phases. Says Holzner: “Geography is important, too. We receive support quickly, and our engineers collaborate smoothly and effectively.”

Stefan Holzner, Senior Technical Consultant & Patents at TGW © TGW

Packing machine © TGW

Pack Chain Reduce © TGW