Tiefe Integration von Robotern in Maschinen und Anlagen
- Automatisierung
- Robotik
- 19.12.2024
- Lesezeit: {{readingTime}} min
- Artikel teilen
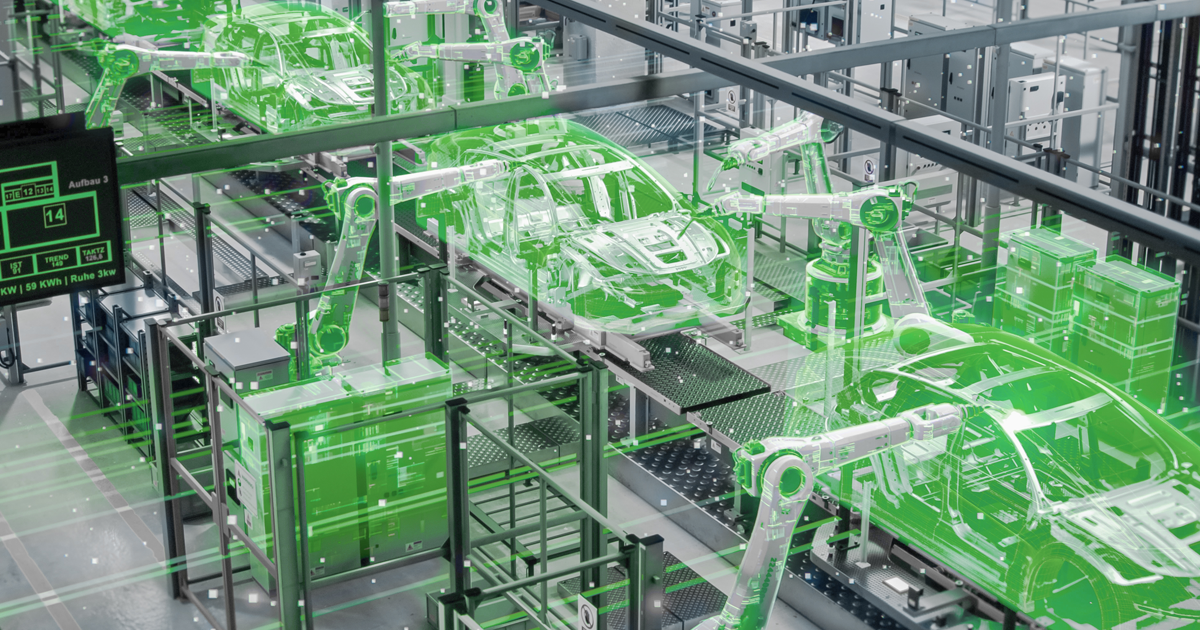
Inhalt
Wann erreichen Standard-Industrieroboter ihre Grenzen?
Typische Nutzer von Standard-Industrierobotern setzen diese zur Automatisierung vielfältiger Aufgaben in Produktion und Logistik ein. Im Fokus steht dabei ein breites Spektrum vorgefertigter Standardfunktionen und Technologiepakete für verschiedene Anwendungen, wie etwa Punkt- oder Lichtbogenschweißen sowie Pick-and-Place. Der Industrieroboter fungiert somit als vielseitiges Automatisierungswerkzeug.
Sind Standard-Industrieroboter immer die richtige Wahl? Nicht unbedingt. Ein weiteres wichtiges Anwendungsfeld der Robotik sind integrierte Roboter in ganzheitlichen Produktions- oder Logistiklösungen. Beispiele dafür sind Maschinen und Anlagen zum Lackieren, Kleben und Schweißen unterschiedlicher Bauteile oder zur Verpackung von Konsumartikeln. Integratoren arbeiten oft im Seriengeschäft und beschäftigen sich jeweils mit einer abgegrenzten Klasse von Aufgaben und Anwendungen, mit dem Anspruch, für Ihre Kunden besonderen Nutzen zu schaffen. Hier sucht man keine Vielzwecklösung sondern optimiert auf die konkreten Bedürfnisse hin.
Anforderung: Perfektes Zusammenspiel von Robotik, Anlage und Prozess
Meistens steht nicht der einzelne Roboter im Vordergrund, sondern die Gesamtfunktion der Lösung. Roboter werden als integrale Komponenten für die flexible Anpassung an ein breites Spektrum unterschiedlicher Produkte verwendet. Sie sollen perfekt mit anderen Komponenten einer Gesamtlösung zusammenspielen.
Im Bereich der Automatisierung solcher integrierter Lösungen waren früher Robotik und Steuerungstechnik (SPS) getrennte Bereiche, sowohl in Bezug auf Anbieter und technische Lösungsansätze als auch auf die Verantwortlichkeiten und Kompetenzen der beteiligten Fachleute. Eine wirklich flexible und moderne Lösung kann jedoch nur durch integrierte Automatisierungstechnik erreicht werden.
Der Wunsch nach tiefer Integration wirft Fragen auf:
Durch den steigenden Bedarf an Integration entstehen immer mehr Fragen wie zum Beispiel:
Welche Faktoren sind bei der Entscheidung zur Integration wichtig?
Wie bleiben die Prozesse entlang des Lebenszyklus – von der ersten Konzeption über die Umsetzung bis zum After Sales – handhabbar und effizient?
Was heißt das im täglichen Einsatz der Lösungen für die Anwender?
Was muss beachtet werden, wenn Hersteller moderne Technologien wie Cloud Computing, Big Data und Datenanalyse nahtlos in die Systeme einbinden wollen – sowohl heute als auch in Zukunft?
Mögliche Lösungen bei getrennten Steuerungen
Es gibt viele verschiedene Antworten auf diese Herausforderungen. Dazu gehören Integrationspakete der Roboterhersteller, die eine enge Verbindung zu Steuerungssystemen ermöglichen, Initiativen zur Standardisierung von Schnittstellen, wie der neue „Standard Robot Command Interface“, und innovative, roboterunabhängige Programmier- und Bedienkonzepte. Trotz dieser Fortschritte gibt es jedoch immer noch zwei getrennte Steuerungen: eine für die Robotik und eine für die Steuerungstechnik. Durch diese Ansätze wird die digitale Kluft zwischen Maschinensteuerung und Robotik bereits teilweise überwunden. Viele Standardanwendungen, wie das Beladen von Maschinen oder die End-of-Line-Palettierung, lassen sich hiermit relativ einfach umsetzen.
Was tun bei komplexen Anwendungen?
Bei komplexeren Anwendungen mit einer hohen Wechselwirkung zwischen Roboter und Umfeld (wie Kleben, Lackieren, Messen oder Schweißen) reichen die bestehenden Lösungen jedoch noch nicht aus. Maschinen- und Anlagenbauer, die ihre Systeme mithilfe von Robotern flexibler gestalten möchten, stehen immer noch vor einigen Herausforderungen.
Funktionales Zusammenspiel: Roboter und Kernfunktion müssen in vielen Fällen nahtlos und präzise miteinander interagieren. Das bedeutet, dass sowohl die Bewegungen der Maschinenteile und Roboter synchronisiert werden müssen, als auch die Prozesstechnik genau auf die Bewegungen des Roboters abgestimmt sein muss.
Teileprogrammierung: Die teilespezifischen Produktionsabläufe (Programme oder Rezepte) müssen sowohl Bewegungs- als auch Prozessinformationen integrieren. Anwender wünschen sich zudem die Möglichkeit, diese Programme mithilfe von Tools offline vorzubereiten, um die wertvolle Produktionszeit nicht durch Teach- und Einrichtarbeiten zu blockieren. Nur so bleiben diese hochintegrierten und effizienten Maschinen für die Betreiber handhabbar und können ihr volles Potenzial entfalten.
Datenintegration: Bei komplexen Produktionsmaschinen und -anlagen entstehen durch die Roboter, den Prozess und die beteiligten Maschinen große Mengen an Daten. Diese müssen in Echtzeit integriert werden, um ein optimales Zusammenspiel sicherzustellen. Gleichzeitig müssen sie bereits in der Planungs-, Engineering- und Inbetriebnahmephase sowie während Service und Wartung eine optimale Informationsbasis sowie eine benutzerfreundliche Bedienung bieten. Zukünftige Technologien wie datengetriebenes Lernen oder Predictive Maintenance können nur dann erfolgreich umgesetzt werden, wenn die Daten verfügbar und konsistent sind.
Bei hoher Wechselwirkung zwischen Roboter und Umfeld stehen Maschinen- und Anlagenbauer vor Herausforderungen.

Mit KeMotion ist eine tiefe Integration der Robotik möglich
Mit KeMotion, dem Robotik-Technologiemodul der Automatisierungsplattform Kemro X, bietet KEBA eine Lösung, die alle drei Herausforderungen – funktionales Zusammenspiel, Teileprogrammierung und Datenintegration – konsequent und durchgängig meistert:
Nahtloses Zusammenspiel: Durch zahlreiche Anpassungsmöglichkeiten zum Beispiel für Roboterbewegungen, Systemverhalten und Schnittstellen können Prozess und (Roboter-)Bewegung perfekt aufeinander abgestimmt werden. Dadurch entstehen durchgängige, einheitliche Lösungen, die neue Maßstäbe in Produktivität, Prozessqualität und Flexibilität setzen.
Teileprogrammierung und Offline-Vorbereitung: Mit der Erweiterungsmöglichkeit der KEBA-Robotersprache KAIRO können Bewegung und Technologie in einem gemeinsamen Teileprogramm abgebildet werden – konsistent und benutzerfreundlich. Dies ermöglicht es, Teileprogramme offline mit einer prozessspezifischen Entwicklungsumgebung am digitalen Zwilling vorzubereiten und trotzdem auch interaktiv an der Maschine anzupassen, um Produktionsprozesse bei Bedarf weiter zu verfeinern. Besonders geschätzt werden der einfache Umgang und die integrierte Berücksichtigung der spezifischen Prozesserfordernisse.
Datenintegration und -handling: Durch das einheitliche Datenhandling zwischen Robotik und Prozesssteuerung sowie optional integrierten Technologiemodulen in Hochsprache stehen für alle datengetriebenen Anwendungen durchgängige und synchronisierte Daten zur Verfügung. Dadurch wird auch der Service und Support für diese integrierten Systeme vereinfacht – von Systemupdates bis hin zur Applikationsunterstützung.
Fazit: Die Verschmelzung von Robotik, Prozesstechnik und Automatisierung für optimale Produktionslösungen
Flexible und moderne Produktionslösungen können nur durch ganzheitliche Automatisierungskonzepte erreicht werden. Damit Robotik und Steuerungstechnik/SPS perfekt aufeinander abgestimmt sind, ist ein funktionales Zusammenspiel von Robotern und Kernfunktionen unerlässlich. Die Teileprogrammierung sorgt sowohl offline als auch online für einen effizienten Ablauf. Ein optimales Zusammenspiel wird zudem durch eine entsprechende Datenintegration und -verfügbarkeit sichergestellt, um zukunftsweisende Ansätze wie Predictive Maintenance oder datengetriebenes Lernen erfolgreich umzusetzen. Technologiefokussierte Maschinen- und Anlagenbauer können mit dem integrierten Automatisierungssystem Kemro X leistungsstarke, hochflexible Gesamtlösungen bieten, die auch komplexe und variantenreiche Aufgaben für ihre Anwender beherrschbar machen.