How autonomous do mobile robots need to be to work efficiently?
- Automation
- Intralogistics
- Robotics
- 20.1.2025
- Reading Time: {{readingTime}} min
- Share Article
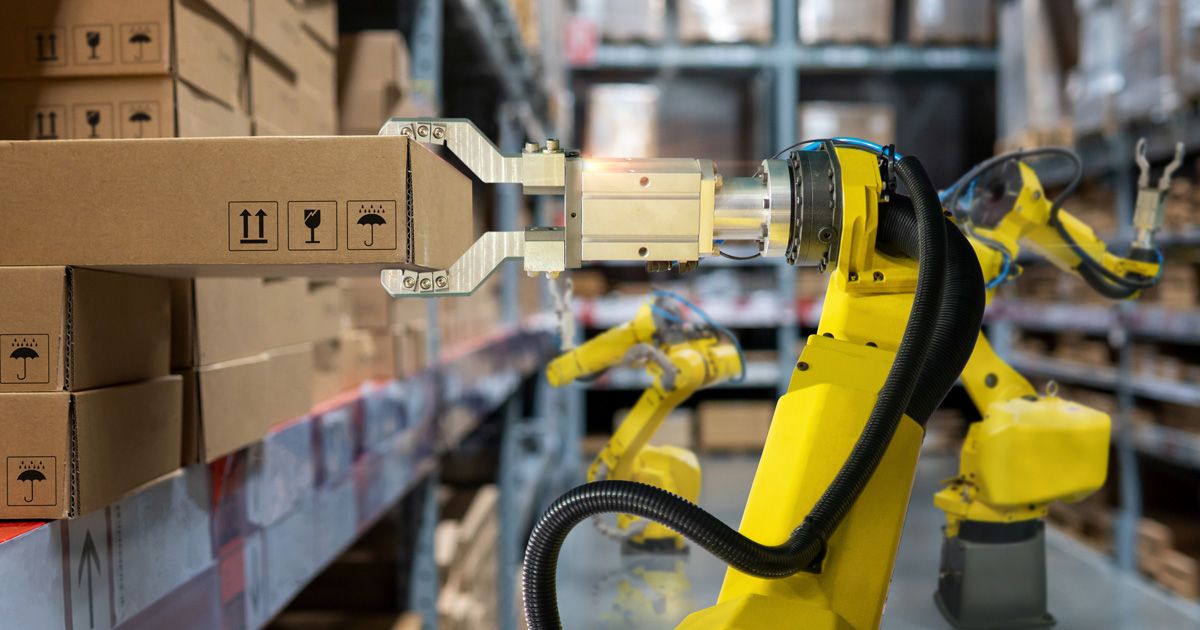
Contents
A mobile robot's autonomy describes its ability to perform tasks without human intervention, with different levels of autonomy. While simple systems execute strictly programmed sequences, advanced robots can make independent decisions and dynamically adapt to their environment with the help of artificial intelligence. Understanding the different levels of autonomy and their differences is crucial to finding the right robot for an application.
Levels of autonomy
Automation: The term “autonomous mobile robot” (AMR) is often misunderstood and confused with “automated guided vehicle” (AGV), although the two terms describe different technologies and capabilities. Many so-called AGVs follow predetermined routes, such as magnetic tapes or inductive lines in the floor. These systems work automatically, but without real autonomy, since their movements are strictly programmed.
Partial autonomy: Other robots use sensors, such as laser scanners, to avoid obstacles. Such systems learn positions and trajectories that they use for their tasks. However, there is no autonomous decision-making ability here either, since routes and processes are defined in advance.
True autonomy: A robot that independently prioritizes tasks, finds alternative routes and takes on additional tasks during transport is considered autonomous.
In my opinion, you can only speak of an autonomous mobile robot when a robot makes independent decisions – often with the support of artificial intelligence.
Andreas Reingruber, Section Manager Intralogistics at KEBA, says: “In my opinion, you can only speak of an autonomous mobile robot when a robot makes independent decisions – often with the support of artificial intelligence. All other forms of movement are merely automated. An example: a mobile robot uses a manipulator to take material from a pick-up point and then bring it to where it is needed. In doing so, it must independently recognize and decide how to adjust the position of its gripper in order to grasp the package in the best possible way.”
This is where technologies such as machine learning and neural networks come into play. These enable the robot to learn from the data in its environment and optimize its actions.
In particular, reinforcement learning, in which the robot continuously improves its decisions based on feedback from its environment, helps it to adapt to unforeseen obstacles and changes. Reingruber: “Only with such advanced technologies can the robot effectively operate in dynamic and complex environments and develop the necessary autonomy.”
What is important in the decision-making process
The choice of the right autonomy level for mobile robots depends on the specific requirements, processes and objectives of a company. To make an informed decision, companies should carefully analyze the following aspects:
1. Process complexity and environment
The more complex and dynamic the processes and environments, the higher the robot's autonomy should be.
Structured environments: In clearly defined and controlled environments, such as production lines or automated warehouses, only medium or low autonomy is often required. Here, robots can work effectively with fixed routes, like automated guided vehicles (AGVs), because the environment has little variability.
Dynamic environments: In more complex scenarios, such as in fulfillment centers, hospitals or agriculture, robots are required to react to unpredictable obstacles, changing requirements and dynamic movements of people or objects. A high degree of autonomy is necessary to adapt flexibly and work efficiently.
Practical example: A robot operating in a warehouse environment may need to pick up goods from dynamically changing positions and find alternative routes to avoid interference when necessary. A system with advanced sensor technology and an AI-based decision-making capability is advantageous here.
2. Requirements for scalability and flexibility
A company's planned scalability and adaptability have a direct impact on the choice of autonomy level:
Future-proofing through modular systems: Robot manufacturers who plan to expand their robot fleet in the future or integrate new processes should consider systems that allow autonomy capabilities to be upgraded. This can be done through modular software or hardware that makes the robot upgradeable to higher levels of autonomy.
Adaptability to new tasks: Robots with higher autonomy can be integrated into new processes more quickly. They do not require extensive reprogramming, but learn to take on new tasks through machine learning and AI.
Practical example: A logistics company can start with a semi-autonomous system because predefined transport routes can be used effectively. If the logistical structures change, it is possible to switch to fully autonomous robots, which can plan their own routes.
3. Human-robot collaboration and cooperation:
In work areas that are frequented by humans, a high degree of autonomy is essential. In this case, robots must be able to reliably detect obstacles, dynamically adjust routes and react to human behavior.
Technologies such as computer vision and predictive analytics play a central role here, as they enable highly autonomous robots to accurately recognize human intentions and react to them flexibly. Without these capabilities, safe and productive use in such environments would not be possible.
4. Technology requirements
The technology built into the robot is also crucial for the degree of autonomy, as it forms the basis for its perception and action skills.
Simple tasks – little autonomy: In logistics centers, mobile robots are often only required or allowed to have a low degree of autonomy because this is more cost-efficient, safer and easier to manage. Structured environments are required for smooth and stable operation. Less autonomous robots do not require expensive sensors or complex AI systems. Instead, they can be controlled centrally and guided along predefined routes, making them easier to scale.
More complex tasks – high autonomy: For robots that are to perform additional tasks such as object recognition, manipulating or interaction with the environment, advanced technologies such as LIDAR, cameras and 3D sensors are indispensable. Likewise, powerful computing units are required to process data in real time and react flexibly to changes.
Practical example: A mobile, autonomous robot for weed control in agriculture uses lasers or hot steam to destroy weeds in a targeted and chemical-free manner. Equipped with cameras, sensors and AI-supported image processing, it independently recognizes weeds, differentiates them from crops and treats them with pinpoint accuracy, without human intervention. Its autonomy enables it to navigate uneven terrain, adapt to changing light and weather conditions, and avoid obstacles such as stones or branches. Reliable and stable operation must also be guaranteed in rain, wind and dirty conditions.
CONCLUSION: Customized autonomy increases competitiveness
Mobile robots have established themselves as indispensable tools in industry and logistics, but their efficiency depends crucially on the degree of autonomy. While simple automation may be sufficient for structured environments, dynamic scenarios require a high degree of autonomy to operate flexibly and efficiently.
The choice of the appropriate degree of autonomy should therefore always be based on a thorough analysis of the process requirements, the environment and the desired scalability. Particularly in complex and changing work environments, highly autonomous systems with AI and machine learning can enable a significant increase in efficiency.
Although the use of such advanced technologies is associated with higher investment costs, a long-term perspective shows that these investments can quickly pay for themselves through lower operating costs, increased flexibility and adaptability. Industries such as logistics could tap into new efficiency potential and increase their competitiveness through the increased use of highly autonomous robots.
Companies that rely on modular and scalable systems also ensure that they have the option to grow with the requirements and to flexibly adapt their robot fleets to new challenges. The transition to higher autonomy is thus not only a technical decision, but also a strategic one.
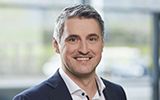