Integrated robotics made easy
- News
- Robotics
- References / Success Stories
- Drive Technology
- 29.3.2022
- Reading Time: {{readingTime}} min
- Share Article
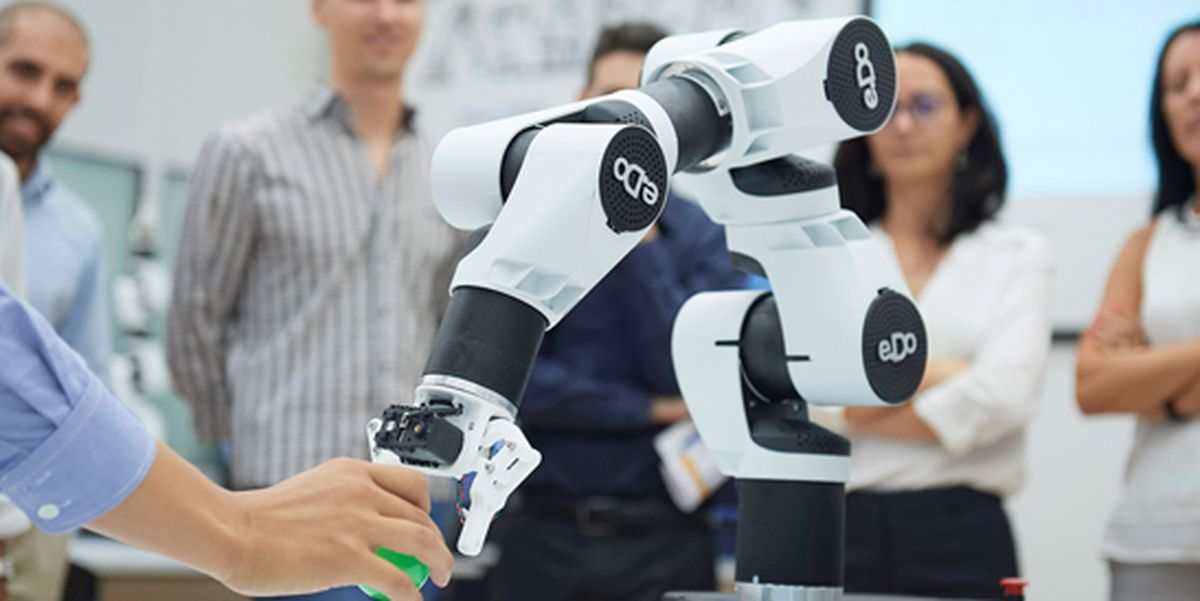
Contents
Comau, located in Turin, Italy, has been developing high-performance industrial robots to integrate and enhance innovative applications in any industrial sector since 1973. Comau robot families range from traditional robotic arms to collaborative and wearable robotic solutions, with various payload capacities, leveraging IoT and AI based technology.
Comau and KEBA have had an intense business relationship since years. The cooperation between both companies started as KEBA developed a fully customized HMI teach panel solution for Comau that met market requirements and excelled with robustness and ergonomics, characteristics which are typical of Comau products.
In 2017 the cooperation was taken one level higher as both parties decided to co-develop and co-market a solution for integrated robotics. The goal of this development project was to be able to control Comau’s wide range of robot kinematics with KEBA's robot solution, KeMotion.
Giulio Scifo, Comau Partner & Sales Development Manager: “There had been many requests to run Comau robot arms with the KEBA system. Above all, customers who already knew KEBA were looking forward to this combined approach, which is unique in its kind and covers an interesting gap in the market." As a platform, KeMotion combines robotics core, SPS Motion, control drives, safety technology and HMI. Comau customers should also be able to benefit from this. The goal was to select the respective robot model at the click of a mouse, and within a few hours it would be ready for use thanks to KeMotion's tools. This is because KEBA not only has IEC robot libraries, but also a ready-to-connect solution: via configuration and parameterization, the kinematics can be integrated into machine logics with just a few clicks.
In order to reach this goal, technical developments were required. Scifo: “Our products had been compatible before, but further adaptations were needed like sharing sensitive data of the Comau robot in order for KeMotion to be fully autonomous in the Comau system. So we started step by step and made incremental changes using two models of 4-axis robots – which was a bit easier than starting with 6-axis robots.” In focus of Comau and KEBA were two main product ranges: palletizing robots and SCARA Rebel-S6 robots. Scifo: “KEBA had been really strong in the packaging industry – that was a true benefit for the development and gave us a head start.” Initial target markets for these robot types were Switzerland, Spain and Italy.
Comau and KEBA tackling customers’ pain points
Not only did both companies co-develop a much sought-after solution, they were also able to address and solve customers’ pain points. One of them being space occupied by hardware in production lines. Scifo: “Very often there are three, four or even five robots in a line, which means you need a control cabinet for each robot."
When using the KEBA system, however, only one control cabinet is needed for the entire line (PLC + robotics). With the "Multi-Rob" feature, up to 16 robots can be operated on one controller, even if they are different types of kinematics.
A second pain point customers have to deal with is skilled employees. “In order to commission and operate a line, you normally need workers with different skills: one employee is handling the PLC and the system and the second one is able to program the robot in the Comau language”, says Scifo.
With the Comau / KEBA solution, one person, who has knowledge of KEBA products and protocols can handle all jobs. Having only one programming language also means time is saved: On average customers will save about a week of training and one day for fine tuning the line before commissioning.
A third benefit of this combined solution lies in the synchronization between line and robot. The entire line now has only one central “brain”, which means one single intelligence to control all machines and axes, including all features like diagnostics.
The cooperation between Comau and KEBA captured in a single word: easy
In the eyes of Scifo, the cooperation so far has really gone very smoothly. “Of course it takes time when two teams join forces and co-develop a new product, they need to get to know each other – also on the technical level. After that was settled, though, we took up speed very swiftly. Especially in the area of sales and marketing we had great synergies and used offered chances as well as we could – this with a superb support from the KEBA team in Italy.” Also here, “easy” seems to be the word that describes the cooperation and the product that results out of it best. Not only is the solution “easy-to-integrate” for integrators and machine builders. The solution is also easy to use, easy to install, easy to maintain, and offers an easy-to-use HMI.
Such a project can be described as “easy” only if the level of expertise is very high – on both sides. “The KEBA team has an enormous technical expertise, a vast knowledge of robotics – in the project we were always on the same page, that is what makes it easy. People at KEBA are passionate about industrial automation, they get as close as possible to their customers”, Scifo emphasizes. According to him, KEBA does not focus on marketing, but on hardcore technical consultancy and fast reaction times - even in tough times or challenging phases in the project - which also applies to the sales team. Scifo explains: “They are very technical and not too pushy, focusing on customer’s pain points. They solve the issue first and then go for closing the deal.”

Giulio Scifo, Comau Partner & Sales Development Manager © Comau

The HMI teach panel solution developed for Comau © Comau

Comau e.DO experience © Comau

Comau Smart Factory © Comau