Deep integration of robots in machines and systems
- Automation
- Robotics
- 19.12.2024
- Reading Time: {{readingTime}} min
- Share Article
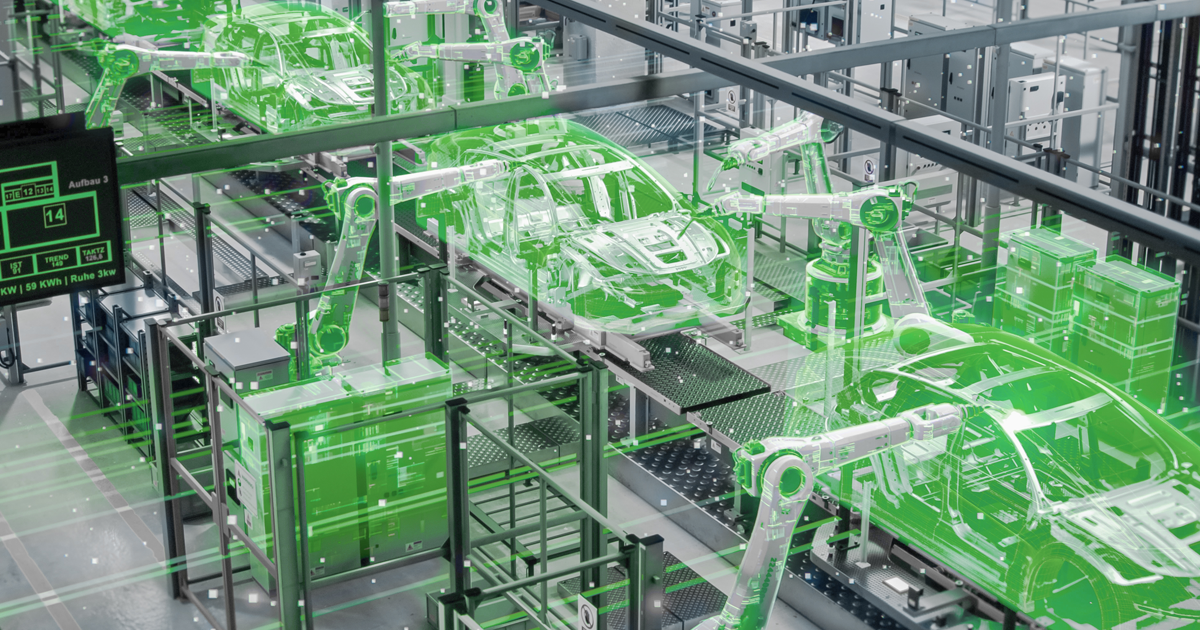
Contents
When do standard industrial robots reach their limits?
Typical users of standard industrial robots use them to automate a wide range of tasks in production and logistics. The focus here is on a wide range of ready-made standard functions and technology packages for various applications, such as spot or arc welding and pick-and-place. The industrial robot thus functions as a versatile automation tool.
Are standard industrial robots always the right choice? Not necessarily. Another important field of application for robotics is integrated robots in integrated production or logistics solutions. Examples of this are machines and systems for painting, gluing and welding different components or for packaging consumer goods. Integrators often work in series production and focus on a defined class of tasks and applications with the aim of creating special benefits for their customers. They are not looking for a multipurpose solution but optimise to meet specific needs.
Requirement: Perfect interaction between robotics, system and process
In most cases, the focus is not on the individual robot, but on the overall function of the solution. Robots are used as integral components for flexible adaptation to a wide range of different products. They should interact perfectly with other components of an overall solution.
In the field of automation of such integrated solutions, robotics and control technology (PLC) used to be separate areas, both in terms of providers and technical solution approaches as well as the responsibilities and competences of the specialists involved. However, a truly flexible and modern solution can only be achieved through integrated automation technology.
The desire for deep integration raises questions:
The increasing need for integration is giving rise to more and more questions such as:
What factors are important in the decision to integrate?
How do processes remain manageable and efficient throughout the life cycle - from initial conception to implementation and after sales?
What does this mean for users in the day-to-day use of the solutions?
What needs to be considered if manufacturers want to seamlessly integrate modern technologies such as cloud computing, big data and data analysis into their systems - both now and in the future?
Possible solutions for separate controls
There are many different answers to these challenges. These include integration packages from robot manufacturers that enable a close connection to control systems, initiatives to standardise interfaces, such as the new Robot Command Interface standard, and innovative, robot-independent programming and operating concepts. Despite these advances, however, there are still two separate control systems: one for robotics and one for control engineering. These approaches are already partially bridging the digital divide between machine control and robotics. Many standard applications, such as loading machines or end-of-line palletising, can be implemented relatively easily.
What to do with complex applications?
However, existing solutions are not yet sufficient for more complex applications with a high level of interaction between the robot and the environment (such as gluing, painting, measuring or welding). Machine and plant manufacturers who want to make their systems more flexible with the help of robots still face a number of challenges.
Functional interaction: In many cases, robots and core functions must interact seamlessly and precisely with each other. This means that both the movements of the machine parts and robots must be synchronised and the process technology must be precisely matched to the movements of the robot.
Part programming: The part-specific production sequences (programmes or recipes) must integrate both movement and process information. Users also want to be able to prepare these programmes offline using tools so that valuable production time is not blocked by teaching and set-up work. This is the only way to ensure that these highly integrated and efficient machines remain manageable for operators and can realise their full potential.
Data integration: In complex production machines and systems, large amounts of data are generated by the robots, the process and the machines involved. This data must be integrated in real time to ensure optimum interaction. At the same time, they must provide an optimal information basis and user-friendly operation as early as the planning, engineering and commissioning phase, as well as during service and maintenance. Future technologies such as data-driven learning or predictive maintenance can only be successfully implemented if the data is available and consistent.
With a high level of interaction between robots and the environment, machine and plant manufacturers are faced with challenges.

KeMotion enables deep integration of robotics
With KeMotion, the robotics technology module of the Kemro X automation platform, KEBA offers a solution that masters all three challenges - functional interaction, part programming and data integration - consistently and consistently:
Seamless interaction: Thanks to numerous customisation options, for example for robot movements, system behaviour and interfaces, the process and (robot) movement can be perfectly coordinated. This results in consistent, standardized solutions that set new standards in productivity, process quality and flexibility.
Part programming and offline preparation: With the expansion option of the KEBA robot language KAIRO, movement and technology can be mapped in a common part programme - consistently and user-friendly. This makes it possible to prepare part programmes offline with a process-specific development environment on the digital twin and still adapt them interactively on the machine in order to further refine production processes as required. The ease of use and the integrated consideration of specific process requirements are particularly appreciated.
Data integration and handling: Uniform data handling between robotics and process control as well as optionally integrated technology modules in high-level language provide consistent and synchronised data for all data-driven applications. This also simplifies service and support for these integrated systems - from system updates to application support.
Conclusion: The fusion of robotics, process technology and automation for optimal production solutions
Flexible and modern production solutions can only be achieved through holistic automation concepts. To ensure that robotics and control technology/PLC are perfectly coordinated, functional interaction between robots and core functions is essential. Parts programming ensures an efficient process both offline and online. Optimum interaction is also ensured by appropriate data integration and availability in order to successfully implement forward-looking approaches such as predictive maintenance or data-driven learning. With the integrated automation system Kemro X, technology-focused machine and plant manufacturers can offer powerful, highly flexible complete solutions that make even complex and varied tasks manageable for their users.