KEBA at SPS 2022
- News
- Events
- 28.10.2022
- Reading Time: {{readingTime}} min
- Share Article
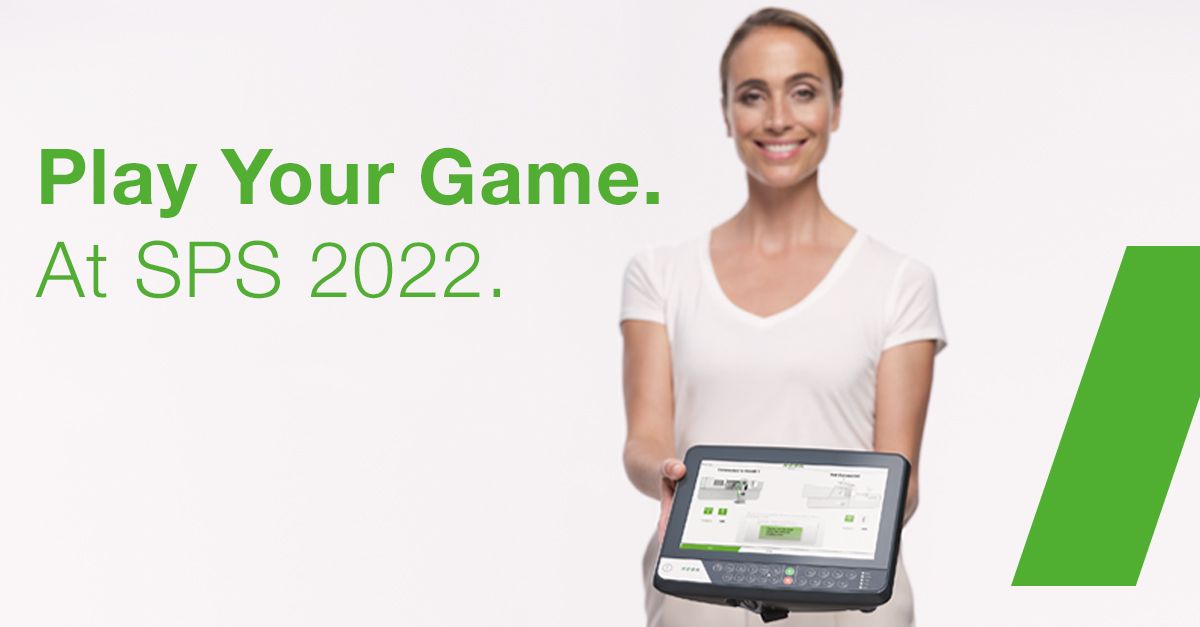
Contents
As a comprehensive provider of automation solutions - from control and operation to drives with matching software - we accompany companies that are looking for or need technological depth and breadth in terms of automation.
In doing so, we listen particularly well to their requirements and challenges in order to be able to offer a solution that is perfectly tailored to them.
We would like to present a few of these solutions to you at the SPS in Nuremberg from 08 - 10 November 2022.
And because we want to continuously develop our products, this year you will have the opportunity to test our operating devices in a playful way and give an immediate feedback. To do so, simply register for a game at our booth and visit us at our exhibition stand.
SPS on air: The digital extension to the exhibition
With the platform "SPS on air", the SPS 2022 in Nuremberg offers a digital program in addition to the physical exhibition.
Visitors and exhibitors will have the opportunity to exchange ideas online not only during the exhibition, but also before and after it.
The pre-heat event on November 3, which ticket holders can attend online the week before the trade fair, will kick off the lecture program with numerous expert presentations on current topics and innovations in the industry.
KEBA contributes to the digital platform of SPS 2022 with the following topics:
1. drag&bot software solution enables flexible robotics
Pre-heat live lecture on Thursday, 03.11.2022 from 14:40-15:00 hrs.
Do we really need a person with special know-how for each and every robot adaptation? Can't the integration of robotics solutions in the production environment be made easier?
In a 20-minute live presentation, Daniel Seebauer, CFO of the software company drag&bot (a part of KEBA Group since fall 2021), will provide an overview of the drag&bot software solution.
This solution enables production workers to quickly and independently implement or adapt robot applications, even without expert knowledge or extensive training.
This is made possible, among other things, by a graphical user interface via which the robot is operated and "programmed" entirely without code. The presentation will explain in detail how this works. More information can also be found in our blog post The most important robotics trends in 2022.
2. Drive-based condition monitoring: Implementing smart maintenance concepts without sensors and the cloud
Live technical lecture including Q&A session on Wednesday, 09.11.2022 from 11:50-12:10 at the VDMA/ZVEI Forum in Hall 3-451
The idea of Condition Monitoring was born more than a decade ago. From the very beginning, it was obvious to most industrial manufacturing companies that knowing the condition of your plant/machine and its central components has a variety of practical advantages as it impacts the optimization of safety, machine efficiency as well as maintenance. Nevertheless, corresponding solutions are still not used on a large scale.
One reason for this could be that the introduction of condition monitoring and the often-associated switch to a cloud solution also always entails a digital transformation of internal processes. The effort involved discourages many companies from moving in this direction.
This presentation will show how easy it can be to implement a local solution for monitoring the status of the engine or drive train and which technical concepts are behind it. You can attend the presentation either live at the VDMA/ZVEI Forum in Hall 3-451 or via stream.
3. The path to a safe robot
Digital round table on Wednesday, 09.11.2022 from 15.00-15.15 and on Thursday, 10.11.2022 from 10.00-10.15 a.m
Safety is becoming a more and more important topic because of the increased collaboration between machines – or robots – and humans in the production process.
During this presentation, you will learn how robots can be safely and fully integrated into various applications for e.g. painting, welding, or sheet metal bending and which selection of directives and standards should be considered.
Our main topics at SPS 2022 at a glance:
1. KeTop Safe Wireless: one control unit for many machines
As companies grow, so do their production lines and machine parks - it is not uncommon for different machine generations from several manufacturer brands to come together. These should be able to effectively communicate with each other, but also be operated in a uniform way.
In the worst case, a production hall that houses ten machines will also have ten hand-held control units in use – with different logic and operating concepts, and without any linking between them. The downsides are not only misunderstandings and operating errors – efficiency also suffers, and cost optimization is completely disregarded – money falls by the wayside.
What is needed is a highly flexible one-for-all-HM solution that is based on the modular principle. If this is then also wireless, machine and robot operators benefit from maximum flexibility and efficiency and operate where they have the best view of the process.
Ideally, such wireless devices have a factory mode in addition to the machine mode (individual machine operation). This means that there is no longer a need for one hand-held control unit per machine, but only one device per service technician/operator.
More information about our wireless control unit Ketop Safe Wireless can be found here.
2. Easy operation and programming of robotic solutions
Requirements for robots are undergoing dramatic changes. Humans and robots are working together more and more frequently, areas that are strongly characterized by manual work are becoming increasingly automated, mass production is replaced more and more frequently by small batch sizes, and individual customizing is in ever greater demand.
But do you really need someone with special know-how for every robot customization? Can't the integration of robotics solutions in the production environment be made simpler?
The answer is: yes, it is possible to implement or adapt robot applications quickly and independently, even without expert knowledge or extensive training. The prerequisite for this is an appropriate software solution, such as drag&bot, with which industrial robots can be easily operated and programmed by production employees.
Kemro X deckt alles ab, was ein Maschinenhersteller für seine Smart Factory benötigt
3. Kemro X – the KEBA automation platform as common coupling
As a complete automation system for hardware and software, Kemro X covers everything a machine manufacturer needs for its smart factory: All mobile and stationary panels, drives and hardware types as well as the engineering tool are built in.
The system has a modular structure and the modules can be used like apps on a smartphone. Modules from KEBA, customer-specific or Linux-based standard modules can be used.
Linux-based openness allows customers to integrate their own software modules as well as third party software to protect. This allows them to protect their know-how and maintain their independence.
The open system architecture enables the required inter-process communication. Following the principle of a modular system, KEBA has developed an extensive range of software units that the machine manufacturer can use for all automation projects: from engineering tools to simulation tools: control engineering, mobile and stationary operating panels, HMI framework, drives, safety technology, motors, I/O units) with extensive expansion cards.
What sets KEBA apart from other automation providers? What are the pain points for machine manufacturers? What will the smart factory of the future look like?
All these questions are answered by Christian Gabriel, General Automation, in an interview about Kemro X.

4. How does artificial intelligence (AI) change control engineering?
Artificial intelligence is already being used in many areas – including private ones – in the course of digitization. It should support people in their daily work.
But to what extent can this technology create added value directly at the machine and in the control system?
Many tasks are now being moved to the cloud due to the high performance requirements, but not all machines have a cloud connection or users do not want this for understandable reasons.
KEBA sees a local AI module in industrial design as a good alternative to the cloud. Combined with the actual machine controller, this opens up numerous previously unused possibilities such as network-independent solutions in the areas of anomaly detection, predictive maintenance and process optimization.
In addition, machines could be equipped with capabilities such as communicating, seeing, thinking and deciding. The use of AI in industry has many advantages: Safe work, faster interpretation of data in advance, increased quality as well as optimized processes – to name just a few.