Extend the mold lifespan and speed up the mold exchange process
- Plastics
- 3.4.2024
- Reading Time: {{readingTime}} min
- Share Article
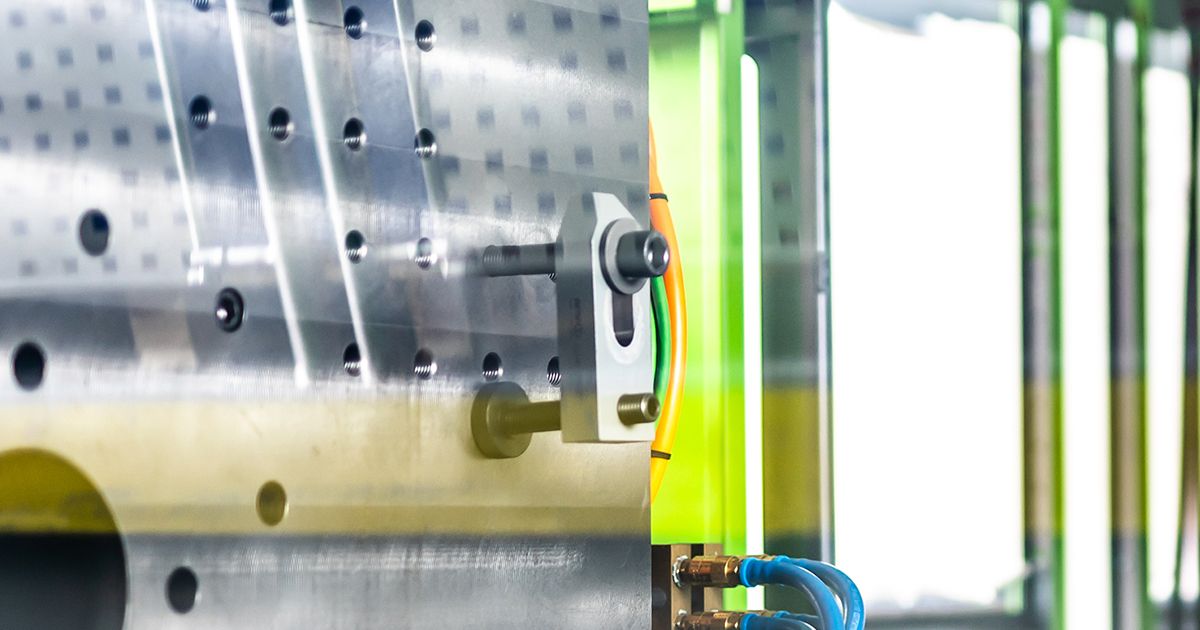
Contents
Mold damages can be a significant concern for plastics manufacturers as they can lead to production delays, scrap or rework of defective parts, and increased maintenance costs.
Furthermore, calibrating a machine after a mold exchange can be a very long and expert-demanding process, machine type independent. Calculating and testing manually requires lots of time and expertise, including many trial-error situations – something the plant’s owners want to avoid in times of qualified workforce shortages.
One alternative for automatically identifying how quickly the mold should close and open at these different stages is the Automatic Ramp Calibration feature commonly available as a part of KePlast Software.

We, humans, learn from our experiences and are able to adapt the parking velocity to protect our vehicles. The same applies to open and close movements of injection molding..
Man vs. machine
A short analogy of this function to daily life is car parking. When thinking of the last curve one needs to take to get to the final parking position, the driver decides at what velocity and with which acceleration the car should move to achieve the smoothest possible movement.
Stepping on the gas peddal and directing the steering wheel in a specific direction to reach the final position too fast leads to problems with immediate need of braking, resulting in pressure overload on brakes, and may move the car slightly forward because of shaking. However, we also do not want to park the car too slowly because there are simply better things to do.
Humans, learn from our experiences and are able to adapt the parking velocity to protect our vehicles. The same applies to open and close movements of injection molding machines, it is, however, not so straightforward to imagine.
Impact of multi-stage mold profile movements on the mold lifespan
The injection molding process's open and close movements usually have three to five velocity stages for mold close and two to five for mold open, each requiring the molds to move at different velocities and with different acceleration or deceleration to avoid unnecessary mold damage caused by excessive braking and shaking.
On the KePlast screen, the horizontal lines show constant velocity, and the steep lines show the change in velocity. Acceleration refers to a change of velocity in time – being that a speed up or slow down. And as a ramp, we consider the linear change of velocity, which can be adjusted with “Start %”, “Mid %” and “Stop %” parameters.
Molds under control - also without active brake control
The changes in velocity are executed through a manually configured active brake control mechanism. It changes the brake valve or servo valve position, the cross-section where oil flows through, after (and before) the cylinder that moves the mold. So, depending on the desired case, the cross-section is either smaller, resulting in higher resistance to the flow of oil and stronger braking effect, or the cross-section is larger, meaning reduced resistance and lower braking effect.
Since the prices for active brake controls are pretty high, not all machines are equipped with them. If there is no active brake control mechanism, therefore, without the valve, the cross-section is either completely open or closed, not usable for active braking. The mold is then only broken by friction or due to the toggle lever. Thus, soon enough, too much oil must stop being pumped.
The good news is that the Auto Calibration feature works perfectly in both cases and is a preferred choice for standard or low-end machines without active brake control.
At the right time, at the right place
Let´s look closer at what actually happens with an injection molding machine when we want a mold to stop at a particular spot at a specific time. The graphic below shows the desired velocity of the open movement (black curves) and the actual measured values of the vector (green curves). When focusing on the braking, the last and crucial phase of the opening process, we can clearly see the negative velocity followed by a positive one – which is a sign of machine shaking.

Now, the machine's first option to avoid extensive shaking is to use an active brake control mechanism with the help of a brake valve. The second and more expensive option is to use a servo valve for which the process experts need to find the correct values and set them up in the control system manually. Eventually, they can use the algorithm calculated and tested values from the KePlast Automatic Ramp Calibration feature.
A KEBA PLC with KePlast Software has a precise, intelligent auto-calibrating function. This function answers the question of how much shaking should be allowed and adapts the processes accordingly.
By evaluating the optimizing criterium, which is, in this case, the oscillation, defined as the shaking at the end of the movement, the robust algorithm identifies the “trade-off “ ramp values with the help of numerous auto-calibration movements like the idle, reference & validation ones.
KePlast Automatic Ramp Calibration - 3 steps:
- Algorithm evaluates the oscillation at the end of the movement (as on the graphic above).
- It then uses the oscillation of a slow movement as a reference (A).
- Then performs numerous auto-calibration movements to identify the most suitable value based on the optimal “Max (B) & Stop (C)” values.

As a result, the algorithm finds the highest possible Max and Stop ramp values highest acceptable oscillation.
Summary: the benefits of KePlast Automatic Ramp Calibration feature
- Smooth movements and smooth deceleration protect the mold from wear.
- Resource savings during the mold change process – instead of hours, it only takes a few minutes, without extensive tests and trials, with just a few clicks, and with little or no involvement of technical experts.
- The maximum braking ramp can be determined without affecting the machine.
- It is suitable for all types of hydraulic machines, including those with servo valves.