How to achieve robot accuracy of less than 0.1 millimeters
- Robotics
- 7.10.2022
- Reading Time: {{readingTime}} min
- Share Article
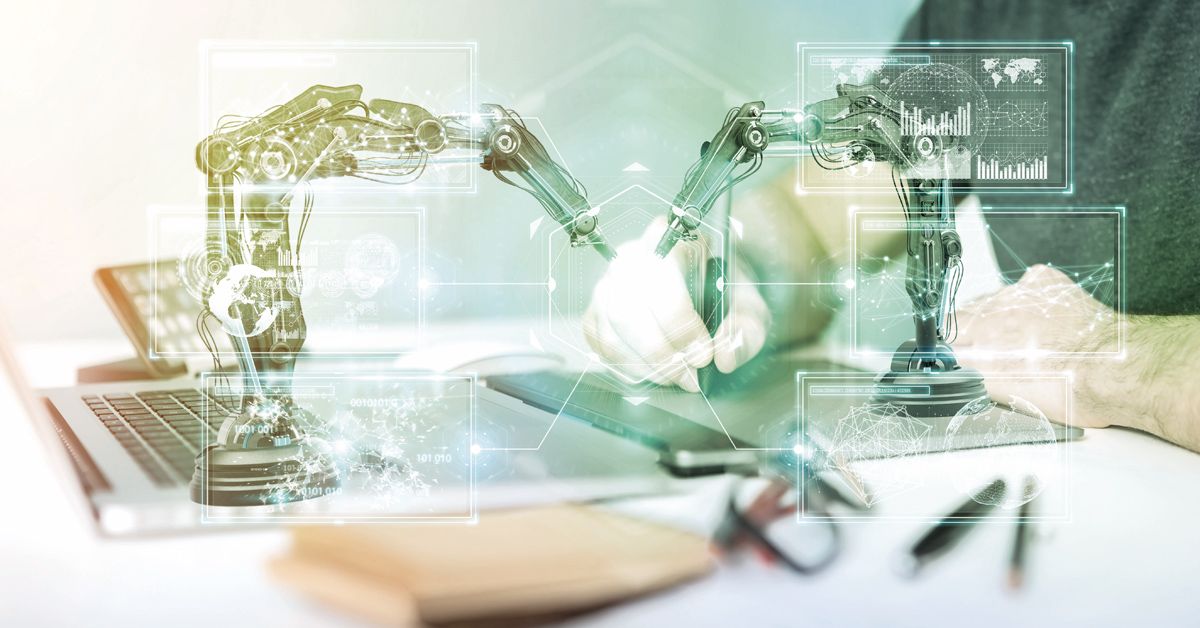
Contents
This article describes how a robot accuracy of less than 0.1 millimeters can be achieved.
Important factors for improving robot accuracy
Since industrial robots made their debut in the 1950s, both the demands and the implementation have changed. Originally, their tasks were heavily focused on repetition, with only low requirements regarding accuracy. But accuracy did improve through lightweight construction, electric servo drives, gearbox design, precision gearboxes with modern controllers and improved path planning. Today, path deviations of less than 1 millimeter are no longer unusual. However, there is a certain saturation as far as adjustments are concerned.
Some applications today require a path accuracy below 0.1 millimeters, for example:
- Laser welding and cutting
- Precision coating and inkjet printing
- 3D printing
Assembly of miniature electronics or aircraft
When looking to increase robot accuracy, engineers for the longest time focused on the mechanical systems in order to get as close as possible to the ideal, the design model.
Today, the focus has shifted to increased computational capacity and more precise measurement technology for improving control. The actual characteristics of the mechanical systems should be captured so that the model can be expanded to include the deviations from the ideal. Focusing on robot calibration and compensation functions pays off, in particular in series production.
Important factors for improving robot accuracy
The creation of a reliable compensation model initially requires engineers to identify the dominant factors precisely. There are many effects that can have an impact on robot accuracy.
Factors impacting accuracy:
- Robot geometry
- Effects of the gearbox, such as transmission, elasticity, backlash on reversal, hysteresis or gear friction
- Limited stiffness due to joint elasticity and bearing errors
- Servo errors
- Vibration
- Higher-order errors
The importance of the various factors in terms of an improvement depends on the robot type. It is very important to identify the dominant factors in each case in order to create a reliable compensation model. It is also true that the more effects need to be taken into consideration, the greater the effort required for the calibration and validation of the compensation functions.
In addition, the drawback of a complex compensation model with many parameters is that it may become unreliable and even counterproductive, causing a marked deterioration of the accuracy. The reason is that each additional parameter entails a new dimension of variations.
Accuracy goals
Characterizing the accuracy of a robot can be complex in itself. There are different understandings of and demands for accuracy, depending on the requirements of the specific application. The calibration and compensation strategies of the robot can vary according to the conditions of the application. Frequently, after taking these conditions into account, the accuracy required for a specific application can be achieved with less effort than one might think.
Static accuracy, repeatability and absolute accuracy
The specifications of common industrial robots usually include values of less than 0.1 mm. However, these refer to static repeatability. This means that a test determines the robot’s precision in returning to a point if the same path is repeated and the robot then stands still.
In practical applications, two other aspects can be important here: the first is the dynamic repeatability that describes how accurately the path is traveled again.
The second is the absolute accuracy. It represents the “ultimate prize” and is interpreted as the robot traveling an entirely new path with new dynamics and adhering to the programmed path within a defined tolerance range.
The path deviations in common robot systems can be higher by several orders of magnitude. A specification must take into account the requirements of the application: is the target a point or a path, will the position of the workpiece be measured relative to the robot, will the paths be repeated or are they different for each cycle.
The goal of efficient accuracy optimization is to expend minimal effort to keep deviations below a certain threshold
Why robot validation plays a key role for accuracy
In order to more easily compare the characterization of robots or even of different robot manufacturers, ISO standard 9283 defines measurement methods and calculation criteria for different aspects of accuracy. The standard contains both static and dynamic parameters. It defines the validation procedure as well as the exact calculation of the accuracy criteria.
These standards hint roughly at the accuracy. However, they are not always adequate for achieving the required level for a specific application. For this reason, other additional factors such as the workspace, speed, the shape of the required movement, etc. should frequently be determined. It is therefore recommended to double-check the accuracy in an application-specific environment.
Toolset for robot validation
The KEBA robot controller includes an integrated toolset in the control software with the tools needed for quick and reliable robot validation. KEBA’s control software can even run on a PC, without any robot. The motion controller simulates not only the setpoint movements but also the robot dynamics as well as the robot behavior.
This makes it possible to examine in advance the forces, moments, and drive currents that occur as well as any deviations caused by controller behavior and gear elasticity. The simulation tools thus help fine-tune the overall mechatronics systems, paths and sequences for greater accuracy. Likewise, users have the option of simulating their core processes in the control system. This allows them to view the overall solution consisting of robotics and process as a whole. Risks during the processing of orders can be avoided from the outset, and even exceptional situations can be mimicked without any expense or risk in order to verify how the system responds.
Nabtesco & KEBA: the most accurate industrial robot in the world
A great example of successful collaboration in the area of robot accuracy is the collaboration with Nabtesco Precision Europe. The cycloidal gear specialist is the first gear manufacturer in the robotics sector to cooperate with a maker of control systems.
The cooperation partners are working together on including the specific characterization data of each individual gear in the design of movements. The goal is to achieve increased performance without higher costs in production. In addition to accuracy, there are many other potential enhancements.
The next goal of this cooperation is a digital replica of the haptic gear with its relevant properties. Model-specific and item-specific gear data is not just important for accuracy, it is also an important building block of Industry 4.0. In addition, the modeling of the gear behavior can also provide significant value with regard to behavior throughout the life cycle.
Conclusion: Increasing accuracy through optimized robot calibration
For a long time, the standard approach for high-precision robots was to optimize precision in manufacturing. However, some applications today require a path accuracy of less than 0.1 millimeters – for example laser welding or coating technologies.
Improved processing performance and measurement technologies create exactly the opportunity needed to enhance the robot model in the control system and thus to increase accuracy.
The goal of efficient accuracy optimization is to expend minimal effort to keep deviations below a certain threshold. Price pressure supports this development.
However, the validation of robots also plays an important role for accuracy, and ISO 9283 defines measurement methods as well as calculation criteria for different aspects of accuracy. The standard contains both static and dynamic characteristics.
Achieving the accuracy required of a robot or for a specific application at minimal cost and effort requires in-depth understanding of accuracy factors and the consideration of all factors such as robot geometry or gearbox effects.
For more information on robot accuracy and robot calibration, download our white paper.