Mobile robots revolutionize logistics
- Automation
- Intralogistics
- Robotics
- 3.7.2024
- Reading Time: {{readingTime}} min
- Share Article
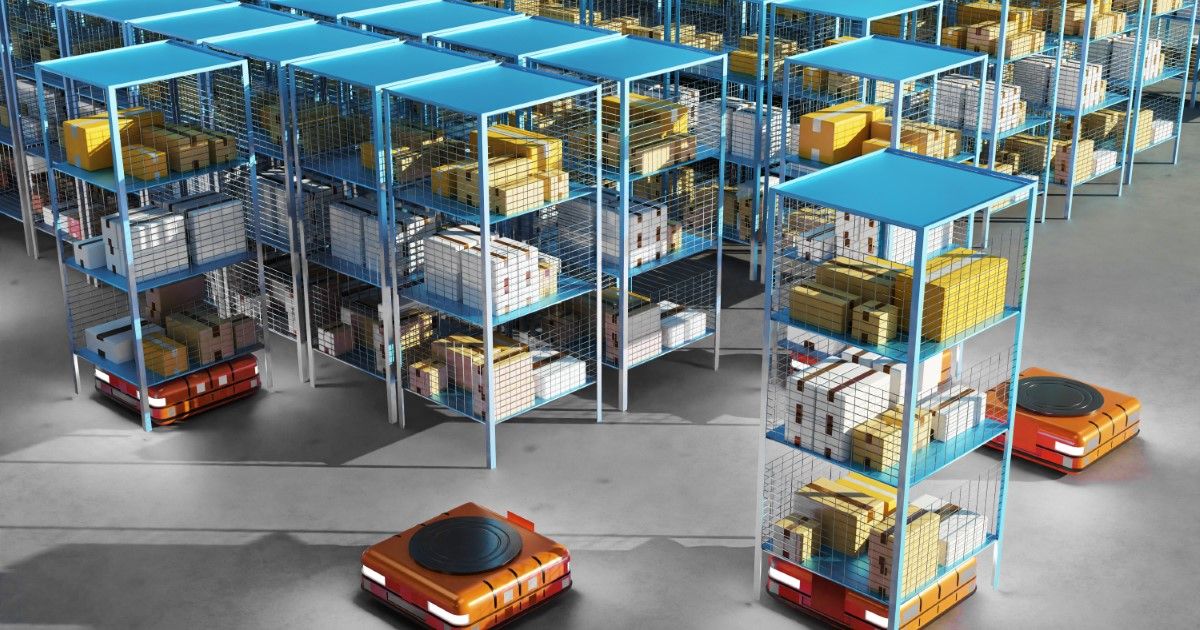
Contents
Those who focused on platform development early on remain flexible and stay in control.
Today’s logistics systems must evolve continuously to reflect the constantly changing consumer habits. Mobile robots allow such flexible adaptations; the trade-off, however, is lower transport speed due to lower throughputs. How can we find the balance between the necessary flexibility and the loss of speed?
Andreas Reingruber, Intralogistics Section Manager at KEBA Industrial Automation, says: “One possibility for achieving this balance is to increase the number of mobile robots in the fleet. However, this only works up to a point. The increased traffic caused by an increasing number of AGVs or AMRs makes the coordination of the vehicles more complex. If vehicles encounter other vehicles at intersections or at loading and unloading stations and therefore need to stop, the entire process becomes less efficient.” (see also Flow rate and density are key to solving jams)
Innovative logistics: mobile robots for intermediate storage
A larger fleet alone is usually not the solution to the problem; a more fundamental change is needed. Both systems — conventional and mobile conveyor equipment — move goods between positions for processing or order picking. However, unlike stationary conveyors, mobile robots provide many more options. They can serve as temporary storage places, or they can prepare tasks for subsequent process steps during transport, such as sorting or picking.
Adds Andreas Reingruber: “The industrial sector has been working on this issue for some time now. A quick solution is to mount a standard 6-axis robot on a mobile robot, which then makes it possible to automatically retrieve goods from warehouses and to load and unload the vehicle. However, such manipulators put strain on the base vehicle, and they need their own infrastructure such as controllers and operating panels.”
The additional weight reduces the running time of battery-operated vehicles. For this reason, mobile robots that are fitted with manipulators should be precisely tailored to their tasks in order to save on weight, duplicate infrastructure and development effort.
In large warehouses with a large variety of fast-moving goods, the use of robot fleets with over 100 vehicles can become necessary. In such scenarios, “Goods-to-Person” robots carry individual warehouse totes to picking stations where the orders are being picked. For greater efficiency, the plan is to develop a mobile robot with a rack superstructure for intermediate storage. It will hold everything that is needed for order picking in a pre-sorted arrangement in the right order. This speeds up the picking process.
An example of order processing with a robot fleet
The mobile robot knows the work order and knows where in the warehouse the bins with the relevant items are stored.
It moves through the warehouse autonomously, retrieves the totes from their storage points and stores them temporarily in its rack superstructure.
On the way, it calculates the shortest route and navigates to the next retrieval position.
Once it has collected all items, it takes them to the picking station, where the transfer is also automated.
All items from intermediate storage are unloaded at once, and the mobile robot is available for its next assignment.
As soon as picking is complete, another robot takes the bins back to free slots in the warehouse.
Ideally, one fleet robot can take on the jobs of as many vehicles as it has storage slots in its intermediate storage rack.
Modular platforms: key to flexibility
Mobile robots are on the rise. This is another reason compelling manufacturers of AMRs and AGVs to offer an even broader portfolio of mobile robots in the future. Those who focused on platform development early on remain flexible and stay in control. The platform is the basis for the development of different types of mobile robots that can be equipped with different navigation systems or object carriers as needed. These add-ons range from simple lifting devices to all-purpose robotic arms. AI supports object recognition and is an optional feature for quality control or for the calculation of gripping points.
Andreas Reingruber: “A modular basic platform can provide the primary functions such as driving and navigating as well as the service concept. More features are added on top of this basic platform — mechanical features as well as software added on top of the existing control systems. The dynamic market situation increases the pressure to come up with flexible solutions in response to changing requirements.”
This article has also been published (in German) in “Robotik und Produktion”, issue 1/2024 (S 56/57).
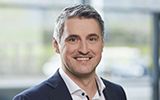